Heating boiler for solid fuel
The cost of a heating boiler made by an industrial method (regardless of the type of fuel, except electric), starts at 13 thousand rubles. These are low-power samples that are able to heat a small country house. Most homeowners are not suitable. In addition, it is not always possible to use natural gas for heating. It is necessary to consider as an alternative solid fuel, waste oil, electricity. For many people, solid fuel is more suitable: wood, coal, briquettes. Craftsmen prefer to make a heating boiler on solid fuel with their own hands. This saves money and hands have something to do.
Main components
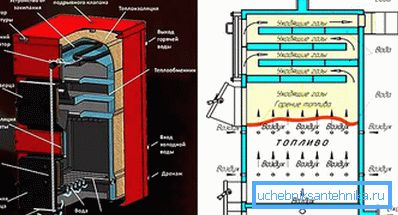
Solid fuel boilers consist of the following components:
- department for loading fuel;
- gold collector;
- throttle valves;
- grate bars;
- water storage tank;
- heat exchanger;
- chimney.
Kinds
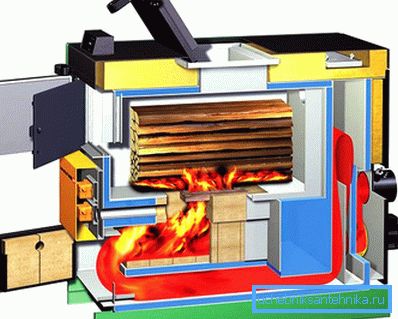
According to the method of placement of the heat exchanger, solid fuel boilers are:
- horizontal - the heat exchanger is located in the horizontal plane;
- vertical - the heat exchanger is installed in the boiler.
A feature of the horizontal location of the heat exchanger is its inclined position. Between the top point and the bottom point (coolant outlet into the system) the difference in level is 1 cm. Boilers with a vertical heat exchanger are mainly used for heating.
In principle, any solid fuel boiler can be used for cooking. For this, it is necessary to provide a cooking surface in its design.
Tools
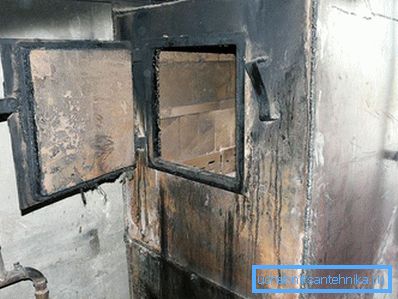
In order to assemble the boiler, you will need tools and materials.
Instruments:
- arc welding machine;
- angle grinder ("grinder") and cutting wheels for cutting metal;
- forceps;
- electric drill with a set of drills;
- level and roulette.
Materials:
- Fireproof brick
- Sifted sand.
- Clay.
- Metal sheet 5–8 mm thick. It is better to use stainless steel, but you can use steel.
- Cast iron grates.
- Metal corner.
- Steel pipes for water of rectangular and round section.
- Doors for the fuel compartment, gold receiver.
- Chimney flap.
- Bypass or circulator only.
If the forced circulation is basic, and the gravitational heating system needs to be saved as a reserve - a bypass is installed. When working only forced circulation install one pump.
Parts manufacturing and assembly
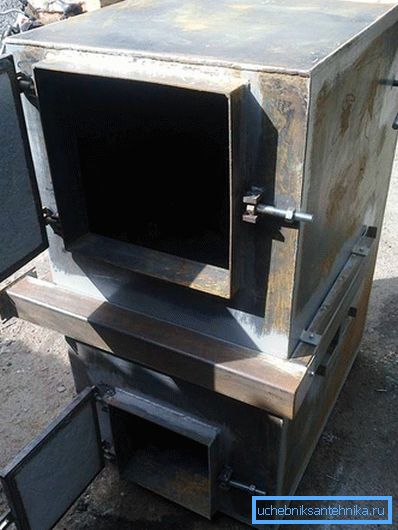
Begin work on the installation of the boiler with their own hands with the drawing up of the scheme and drawings of the assembly. According to them sizes are applied on sheets of metal. By marking cut out the front, rear, side walls and the bottom of the boiler. In front of the cut out openings for the doors of the fuel and gold receivers.
If you cut the openings with a gas cutter, then so that the steel does not “lead”, holes are drilled through the corners of the workpiece, then metal is cut from the middle to the edges along the marking.
If you use the grinder, the holes in the corners of the drill is not necessary. Just cut through the metal on the intended contour. Also according to size, all metal parts of the boiler are cut.
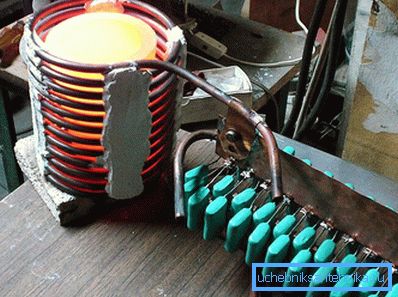
The installation of the heat exchanger begins with making holes in pipes designed for racks. They have a square cross section of 40? 60 cm. In vertical pipes, which are located in front, 4 holes 5 cm in diameter are cut out with a gas cutter, placing them evenly along the entire length of the workpiece.
Round holes of 4 and 5 cm in size are made in the rear pillars. From the bottom of the future heat exchanger, holes are made to supply water to the boiler (return), and from the top - to supply water to the heating system (supply). All openings should be smooth without the influxes, which are eliminated with the help of the "grinder". Welding pipes into a whole produce, maintaining the angles of 90? both vertically and horizontally, brewing the end openings of rectangular pipes (racks).
Welds of the finished heat exchanger are checked for leakage. For this purpose, the return line is temporarily silenced (so that the water does not flow out), and through the flow is filled with water.
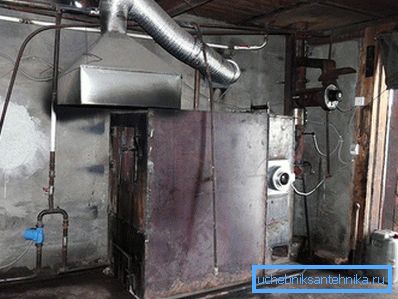
Mounted boiler in the place where it is planned to install it, because all the details are very heavy and moving it in the finished form is problematic. A refractory foundation must first be equipped. It is laid out of refractory bricks. In order for the masonry not to disperse, it can be reinforced with metal corners on the edges and the bricks between each other to cement the mortar. The second variant of the foundation is a monolithic concrete “cushion”.
The dimensions of the foundation should be slightly larger than the base of the boiler. A steel billet is placed on the foundation - the bottom of the ash bin.
The walls of the tank in which the heat exchanger is installed are laid out on it from refractory bricks, a fuel bunker and an ash receiver are equipped. The distance between the heat exchanger and the wall is 1 cm. Grate bars are installed at the bottom of the fuel bin. In the front brick wall there are openings for the fuel receptacle door and the gold receptacle door.
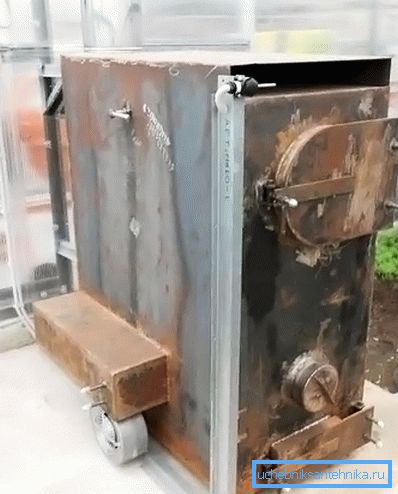
The outer walls of the boiler are sheathed with metal, which is interconnected by corners arranged vertically. Doors are attached to the metal casing. To remove carbon monoxide gases mounted chimney. How to install this node depends on the presence or absence of the cooking surface.
If the boiler will be used for cooking, the chimney is mounted on the side, otherwise - on top of the boiler.
At the exit of the boiler, the chimney is equipped with a gate valve to regulate the thrust. The material for the pipe can be different: fireproof brick, metal, asbestos. The main thing is to achieve the desired level of traction in order to organize the burning process.
For the safe operation of a solid fuel boiler, you can install an open expansion tank, traction and water temperature sensors, and a fan.
In order to prevent overheating of the coolant and explosion of the boiler, it is necessary to constantly monitor the water level and the temperature of combustion. If you use only forced circulation, then at shutdown of electricity during operation of the boiler the risk of explosion of the heat exchanger increases dramatically. Be careful.
Video
In the provided video material, you will be able to visually get acquainted with the design of the solid fuel boiler:
Blueprints
In the drawings, you can consider the design features of a solid-fuel heating boiler:
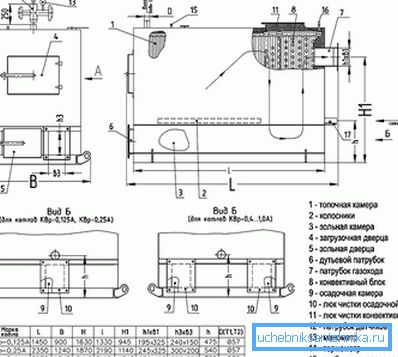
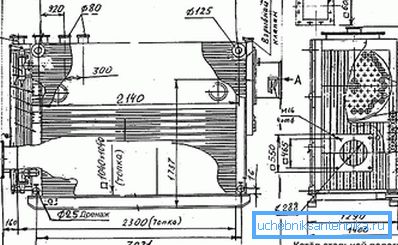
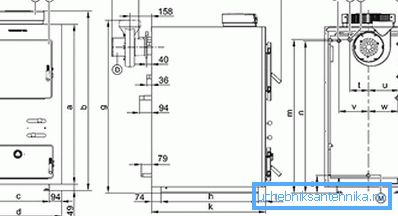
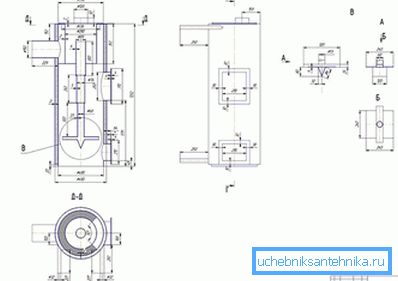
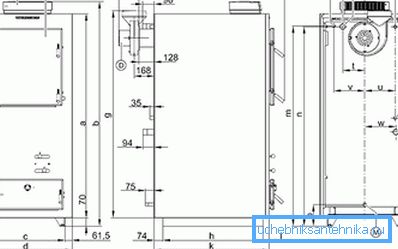
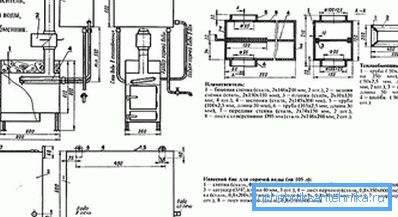