Pyrolysis boiler itself
Unfortunately, such a blessing as natural gas is not yet available to everyone. Very many localities are not gasified. In such a situation, people use electric or solid fuel boilers to heat their homes. The first are costly due to the high cost of electricity. The disadvantage of the second is a very low efficiency: almost half of the heat "goes" into the atmosphere. Increase the beneficial effect and save heat will help the process of pyrolysis. Boilers that work on this principle are called pyrolysis boilers. Since industrial designs are quite expensive, people with the profession of a welder, versed in drawings and able to work with tools, prefer to make a pyrolysis boiler with their own hands.
Principle of operation
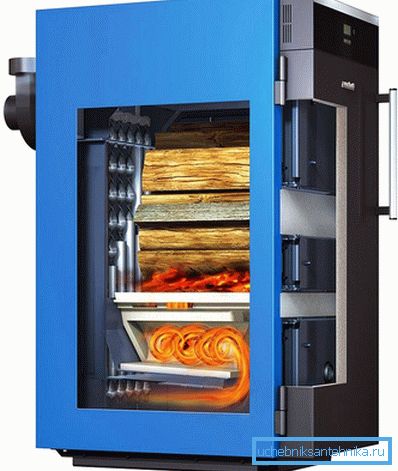
The pyrolysis boiler is essentially a solid fuel heating device. It can work on wood, coal, briquettes or pellets. For each type of fuel make their own calculations.
The general principle of operation is that all fuel burns with a limited access of air. It is served as much as is required for minimal burning with the release of gas, in which volatile hydrocarbons and carbon monoxide are present. The gas obtained in this way gets into another chamber, mixes with the air and burns there, emitting a tremendous amount of heat. Due to this method of fuel combustion, there is practically no ash or emissions to the atmosphere, and the heating of the coolant lasts up to two days on one load.
Components
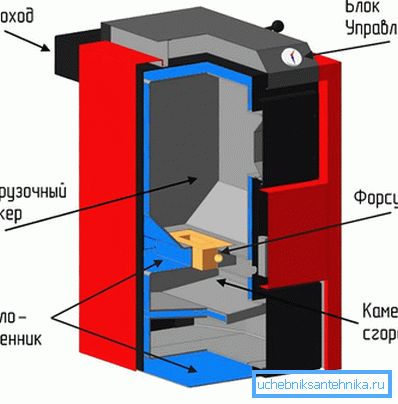
The device pyrolysis boiler consists of:
- offices for loading of fuel - a fire chamber, with a door;
- re-combustion chambers - the gas emitted in it burns;
- blew, in which ash accumulates;
- the bottom door, which closes the combustion chamber of gas and blew;
- nozzles through which the gas enters the combustion chamber;
- chimney for removal of combustion products with a flap for controlling combustion;
- a fan that supplies air to the re-burning chamber;
- grate bars;
- dampers for air supply to the furnace;
- openings for cleaning of a deposit in a copper;
- draining water from the boiler;
- output pipes for supply and return of the heating system;
- thermal insulation of the boiler body;
- safety equipment, which includes thrust sensors, pressure gauge, thermal sensor.
Sequence of work
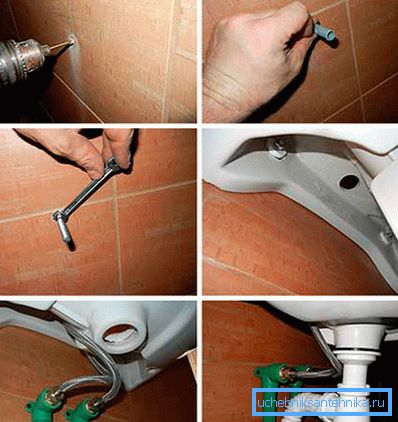
Before starting work on the manufacture of the boiler should consider how to do it right. Usually they start with the execution of calculations, without them drawing up an assembly scheme is impossible. It must be said that mistakes at the stage of calculations can later turn into incorrect operation of the boiler, just as an incorrectly made unit can be dangerous. If you make the calculations and the drawing itself does not work, then you can order this work to specialists.
According to the drawing, metal blanks of the boiler are made. To do this, you will need metal with a thickness of 5 mm for the internal structure and 3 mm for the hull plating. We also need pipes in which heated air will circulate, because of this the heat carrier is heated. You will also need a chimney, dampers, doors, fiberglass seals, a fan. All this can be bought in the store.

For thermal insulation of the re-combustion chamber, fireclay bricks should be purchased. The insulation of the boiler body is made of materials that keep heat well and foil film.
For example, consider the manufacture of a boiler at 25 kW. From metal we cut out blanks of such sizes:
- The outer walls of the boiler body: front and rear dimensions of 1039? 618 mm, side dimensions of 1039? 880 mm, top and bottom dimensions of 880? 618 mm.
- In the front outer wall of the boiler we make rectangular openings for the furnace and ashpit, which are located in the center. The dimensions of the furnace door are 400 × 400 mm, the furnace hole itself is 350 × 350 mm. The dimensions of the door do more, because it is necessary to provide a place for the groove in which the seal will be laid. To simplify your life, you can buy a ready-made door of the right size. Have a hole at a distance of 108 mm from the top of the workpiece. The outer dimensions of the ash pan door are 400 × 200 mm, and the hole dimensions are 350 × 150 mm. Have a hole at a distance of 88 mm from the bottom of the workpiece. Also on the front wall of the boiler there is a rectangular hole for air intake and oval holes for the handles of the dampers regulating the air supply to the afterburner chamber and the flue.
- In the rear outer wall of the boiler make a hole for the chimney, which is placed in the center. Its size depends on the diameter of the chimney pipe. Before starting work on assembling the boiler, it is purchased ready assembled with a valve.
- On the rear wall horizontally at a distance of 202 mm from the center and vertically, at a distance of 373 mm make holes for the return of coolant to the heating system. Its dimensions depend on the diameter of the existing heating system.
- Outputs are also provided for the entry of cold water into the boiler and for the supply of hot water to a protective heat exchanger. The diameter of the outputs of these pipes 3/4 inch. Position them horizontally at a distance of 200 mm from the center. The vertical supply of hot water is located at a distance of 725 mm from a clean floor. The distance between the hot and cold water supply is 255 mm. Also horizontally at a distance of 145 mm from the center and vertically at a distance of 990 mm cut out the feed holes, while providing for the placement of a nozzle for the security group.
- Horizontally at a distance of 198 mm from the center and vertically at a distance of 980 mm a half-inch hole is cut out for the thermal fuse sensor coupling. At the bottom of the workpiece at a distance of 137 mm from a clean floor in the center make a hole for the emptying pipe and expansion tank diameter?.
- In the workpiece for the top of the boiler make holes for the output controller of the boiler circuit. The dimensions are standard, since it is purchased in finished form before the boiler is assembled. The total height of the boiler from the clean floor to the top of the controller should be 1190 mm.
- Cut out from the metal profile U-shaped legs for the boiler with a length of 765 mm.
- From the metal sheet with a thickness of 5 mm, the inside of the boiler is cut in dimensions (w? R? C): furnace 468? 780? 346 mm, afterburner chamber 468? 780? 256 mm, ash pan 468? 780? 250 mm. The upper furnace billet is made longer to weld the heat exchanger tubes. Accordingly provide a place for holes. The same is provided in the bottom billet ash.
- A rectangular opening for a nozzle 130 × 200 mm is cut out in the bottom blank of the flue compartment.
- Pipes with a diameter of 50 mm for a heat exchanger are cut to a length of 730 mm, in an amount of 4 pcs.
- Cut the pieces of pipe for the supply of supply, return, hot and cold water. The diameters of the pipes are selected in accordance with paragraph 1, and the length is indicated in the diagram.
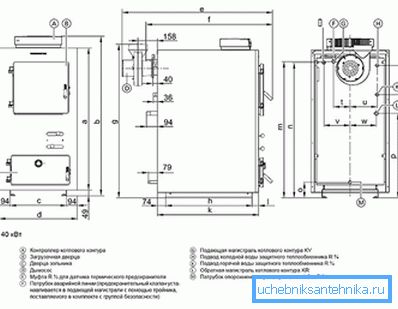
Parts cut to size with the help of arc welding are combined into a single structure in accordance with the scheme.
The holes for the pipes are cut out with a jigsaw (the boiler is assembled at home). Fasten the chimney with a latch. Its extreme point should be at 1289 mm removed from the edge of the handle of the furnace door. From the edge of the funnel funnel to the same handle should be 1101 mm. The inside of the gas combustion chamber is bricked up with bricks. Also isolate the chamber door.
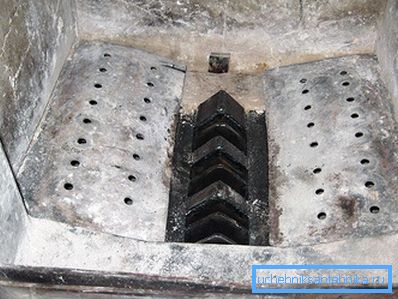
When the metal parts of the internal structure are assembled on the struts, the external case is welded. Spacers are needed in order to avoid deformation of the metal. Doors, automation and everything that is necessary according to the scheme and in accordance with the dimensions specified in it are attached to the finished boiler. The boiler legs are positioned at a distance of 41 mm from the front outer edge of the boiler. The distance between them in width should be 430 mm. The finished boiler is wrapped in thermal insulation and put on a decorative case.
Some nuances
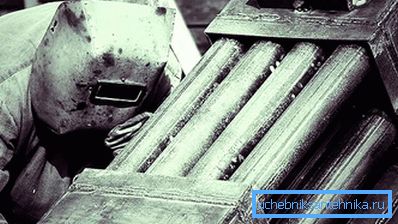
If everything is correctly calculated and collected, then there will be practically no smoke from the chimney. There are some other nuances:
- The dimensions of the boiler depend on its capacity.
- The furnace of a homemade boiler is made slightly higher than that of industrial boilers.
- The configuration of the furnace hopper is best done rectangular.
- To control the amount of fuel and air, you must make a limiter. It is made of a pipe with a diameter of 76 mm and a length slightly longer than the boiler. A disk is welded to the bottom of the stopper, which has a four-centimeter gap with the pipe walls, and a hole is made for it in the boiler lid.
- The coolant pipe is made with a bend for greater heat transfer.
- The amount of coolant entering the boiler is controlled by a valve installed outside the boiler.
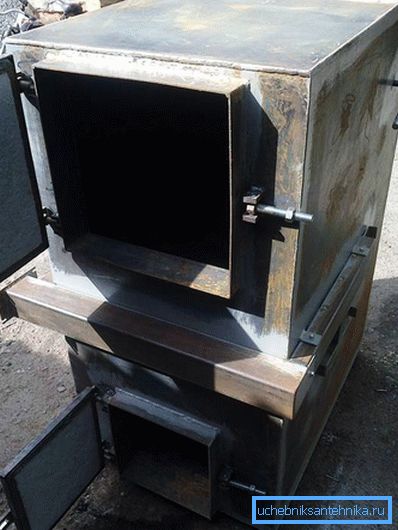
So, the pyrolysis boiler is ready. Maybe you have personal experience in the manufacture of such a device for heating a house. Well, we will be grateful to you for the valuable instructions set forth in the comments to the article.
Maybe you will be interested to get acquainted with the accompanying materials of our site:
- Features of the condensing boiler
- Features of the choice of heating radiators
- How to make a boiler room in a private house
- What is vacuum radiators
Video
How to make a pyrolysis boiler 15-25 kW? You can find out about this by watching the video:
Scheme
Thanks to the schemes, you can better understand how the pyrolysis boiler works and what are its advantages over analogues:
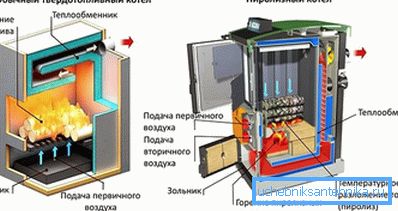

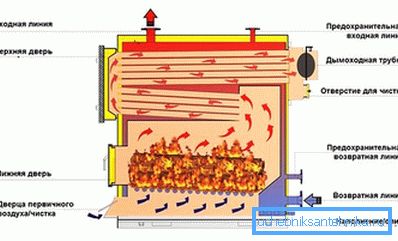
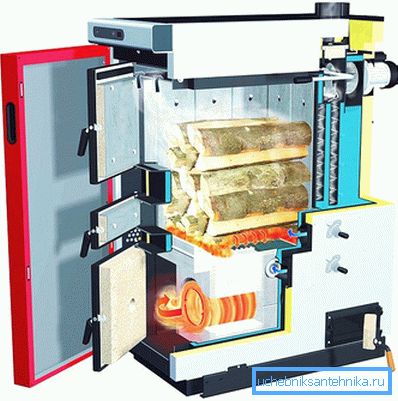
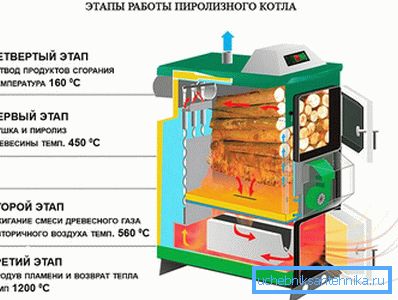