What and how to make a machine for bending a profile pipe:
When assembling various metal structures from shaped pipes, a curved part may be required. Due to the high strength of the profile pipes for bending, it is very difficult to bend them, so a special device is used to perform this operation. In this article, we will look at how to assemble a manual machine yourself for bending a profile pipe, which will be quite enough for household purposes.
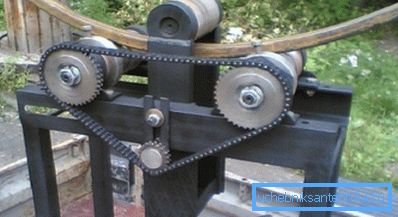
Device design
Principle of operation
Any equipment for bending of the profile pipe ensures gentle deformation, thanks to which the part after bending retains its strength characteristics. In addition, the device allows you to get a certain bend radius.
The type of machine in question operates on the principle of a rotary press. The bottom of his plate form two rollers. The upper slab is the third roller located in the middle between the two lower ones. Therefore, such devices for bending a profile pipe are also called three-roll pipe benders for bending pipes.
The distance between the two lower rollers determines the bend radius. Moreover, they work as a conveyor, moving the part through the deformation zone. The upper drum presses the part, ensuring its bending.
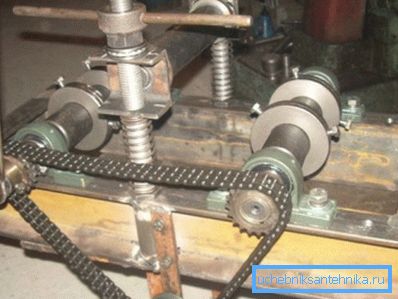
Layout Features
Self-made machines for bending the profile pipe are of two types:
- With the lower feed roller;
- Top feed.
The top feed is used in manual pipe benders, since it is realized with the help of a clamp, i.e. threaded method. The lower feed is carried out in machines, where the clamping force is generated by a hydraulic drive or a jack.
Thus, the machine with the lower feed is more powerful and productive. However, it is much more complex in execution, therefore, if the device will be used for domestic needs, then it is more expedient to perform a machine for bending the profile pipes with your own hands with the top shaft feed.
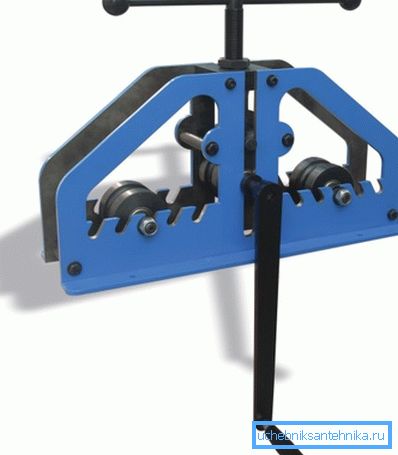
It should also be noted that the shape of the transport rollers affects the device performance.
She may be:
- Smooth - in the form of a cylinder;
- Profile - in the form of a cylinder with grooves for the pipe.
The profiled rolls for pipes are able to bend several parts at once in one pass, which is important in the mass production of metal structures. Since the processing speed is not so important for "home" machines, they are usually equipped with smooth rollers, the price of which is lower.
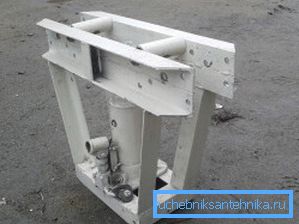
Machine making
Main nodes
Before you make a device for bending a profile pipe with your own hands, you should consider its main elements of which it consists. So, the machine includes:
Stanina | It is the basis of the entire device, to which other parts are attached. As a rule, it is a rectangular metal structure. |
Conveyor | It consists of a pair of rollers, which are fixed on the frame. |
Bracket | Contains guides for the upper drum. |
Upper shaft | It is fixed in a metal U-shaped casing. |
Clamp | Screwed into the bracket and fixes the position of the casing with the upper drum. |
Assembly of the bed
Begin manufacture of the machine with your own hands with the assembly of the bed. As a rule, for these purposes four channels are used, from which the parallelepiped is assembled. Installation of all parts of the metal is carried out using electric welding.
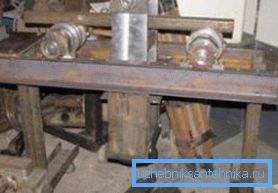
Conveyor assembly
After the bed will be ready, you can proceed to the assembly of the conveyor.
The work is done in this order:
- The first step is to prepare two identical clips. You can find finished parts, or order them in a turning shop.
- Then the brackets need to be welded to the frame into which the rollers will be inserted.
- Next, a bolt is inserted into the hole of each pair of brackets, which serves as an axis for the roller. The shaft is put on the bolt, after which the axis is fixed with a nut.
- On one side of the rollers, chain gears are welded.
- Between the rollers, it is necessary to install a chain tensioning system, which is a flat bracket with a small roller and gear. Moving the gear up or down, you can adjust the tension of the chain.
- At the end of the work on the conveyor, a handle with a lever should be welded to one of the rollers.
Tip! It is desirable to acquire gears immediately with a chain so that there are no problems with incompatibility of parts.
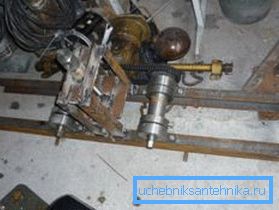
Clamp assembly
The final stage of work is the assembly of the clamp, which is performed in the following order:
- First of all, the legs of the U-shaped bracket, which consist of four profiles, are welded to the frame. The gap between them should be 42-43 millimeters.
- Then, a small U-shaped bracket is made, which is welded from a 40-mm profile. The legs of the structure are drilled holes for the axis of the shaft. The height of the legs should be several centimeters larger than the diameter of the shaft.
- Next, the assembled bracket with a roller must be inserted into the gap between the legs of the large bracket. The small bracket should move freely in a large up / down direction.
- The upper bracket is welded to the legs of the large bracket, in the center of which a hole for the nut is drilled.
- Further, a nut is welded into this hole, into which the pin is subsequently screwed. It is advisable to secure the stud in the bottom bracket, while ensuring free rotation. This will allow to fix the upper drum in different positions.
Tip! Before proceeding to the manufacture of the machine, it is desirable to complete the drawing, this will avoid errors in the installation process.
This work on the design is completed. It should be noted that machines made in a similar way for bending a profile pipe with their own hands are not inferior to similar proprietary devices, the cost of which is very high.
Conclusion
With at least a little experience with metal and welding machine, you can independently perform the above device. As a result, such a homemade machine for bending a profile pipe will allow to obtain curved parts that may be needed for a variety of household needs. From the video in this article, you can get more information on this topic.