Butt-weld pipe welding: technology and equipment
This article is about how to perform butt-weld pipe welding. It does not pretend to be complete: it is only the author’s attempt to present her knowledge and practical experience, adding it to the baggage of the reader’s knowledge. We have to get acquainted with some of the nuances of technology and equipment used for welding.
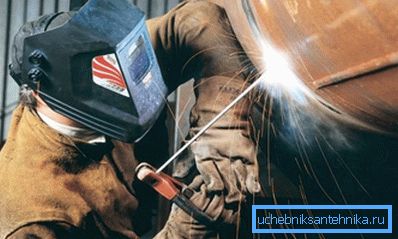
Types of pipes
Which of the popular materials used in the construction of pipelines for various purposes, butt-boiled?
- Steel. For their connection in the field using gas (acetylene) and electric, or arc welding of the pipe joint.
However: standpipes of water supply, for example, where it is better to cook with gas with sleeves - socket connections. Melt welding wire fills the space between the inner surface of the sleeve and the outer surface of the pipe; due to the greater thickness of the seam longer able to resist corrosion.
- Plastic. To be precise - polyethylene and polypropylene pressure. Much less common (and, accordingly, brewed) exotic like polybutene (PB) or polyvinyl denfluoride (PVDF). At the same time, welding of pipe joints is used mainly for pipelines of large diameters; for small sections, coupling joints are used.
Steel
Let us examine both methods of welding steel pipelines.
Gas
The main tool of the gas welder is an apparatus consisting of a burner, cylinders - acetylene and oxygen - and high-pressure hoses.
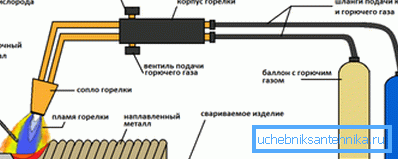
Of the protective equipment required glasses and a suit of dense flame-resistant material. For cutting and fitting parts, the burner can be replaced by a cutter that differs from the burner by the presence of a cutting tap (it allows you to create a narrow stream of oxygen under high pressure inside the torch).
How do you weld the swivel pipe joints?
- The burner is adjusted to a stable torch with a bright even glow along the entire length. Smoky and dark, with blue, the flame is equally useless: in the first case, acetylene does not burn completely due to the lack of an oxidizing agent, in the second - an excess of oxygen again leads to a drop in temperature.
- The ends (preferably with chamfers removed) are heated in a small area until the moment when the steel is melted.
- The welding wire is brought to the gap between the welded ends, and the melt drops from it are blown to the surface of the melted end, creating a bridge between the parts to be joined. By displacing the reflow zone, the welder forms a uniform seam around the entire circumference.
How is the welding of fixed pipe joints near the walls and other structures that do not allow to enter from the rear?
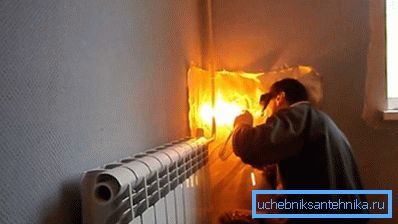
- With the help of an ordinary mirror. It is installed so that the back side of the pipe is visible.
The main problem here is that it is difficult for the welder to adjust to the specularity of the visible movements; the ability to come with a long experience. If for the first time you are trying to weld a fixed seam with your own hands, do not try to do this work with the help of a mirror.
- Through a window cut in the front side of the pipeline. The back side of the seam is boiled inside, after which a fragment of the window is bent to its original position and brewed.
How is the notorious sleeve welded? Yes, just like a butt joint. The only subtlety is the high-quality heating of the pipe inside: in order for the connection to be strong, its surface must be melted.
Electric
Here the tools are a welding transformer, an electrode holder and a pair of wires. Protective equipment requires dielectric mittens, a suit made of dense non-combustible material and a mask with darkened glass (see also Polymer pipes article: how to choose a suitable material for the construction of engineering networks).
Note: the electric arc radiates in a very wide spectral range. An essential part of the radiation is ultraviolet. Attempting to cook at the glance, without glasses, will cost you a sleepless night because of the strong cracks in the burned retina; the person will also receive severe burns similar to those of the sun.
The essence of the method is in the creation of a constant or interrupted arc between the electrode and the parts being welded, arising due to the fact that the transformer creates a significant potential difference. The arc melts the edges of the parts to be joined; at the same time, the metal of the electrode is transferred to the welding field, forming a seam.
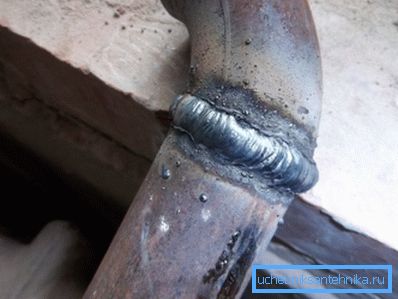
Actually, the art of the welder for the most part comes down to the ability to maintain the arc, preventing the electrodes from sticking to the parts with a low welding current or burning them with an overestimated one.
Welding electrodes are provided with a coating of non-conductive material.
Its function is twofold:
- The coating serves as the dielectric that allows you to ignite the arc of the discharge. Otherwise, the welder would have to keep the burning electrode at a constant distance from the seam, which, you see, is unrealistic.
- In addition, it, when burned, forms slag on the surface of the weld, thereby protecting the molten metal from excessive chemical activity of atmospheric oxygen. Burning out of carbon at metal boiling, for example, is quite capable of making the seam overly ductile. After cooling, the slag, which has low mechanical strength, is easily removed from the surface with a hammer, pick or cleaned with a grinding machine.
Security
What basic safety measures should be observed when performing welding works with gas and electric welding?
- Keep the tip of the burner or torch clean. Its clogging with metal splashes can lead to a reverse impact with the explosion of the gas mixture in the hoses.
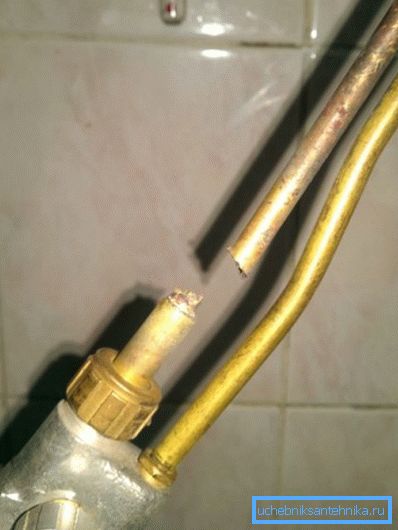
- Ensure tightness of connections at fittings. The leakage and ignition of acetylene (or propane, which is used for cutting metals) can damage both hoses, which in a closed room will lead to a rapid accumulation of an explosive mixture.
- To monitor the absence of leakage on the cranes of cylinders during operation and storage. What is the reason for this instruction - I think you can not explain.
- Avoid working in oiled clothing, and especially in oiled gloves. For the ignition of fuels and lubricants do not even need a flame: enough contact with pure oxygen.
- When moving cylinders, use stretcher or trolley. A cylinder falling down by a valve is likely to turn it into an uncontrollable rocket projectile weighing a little less than a centner.
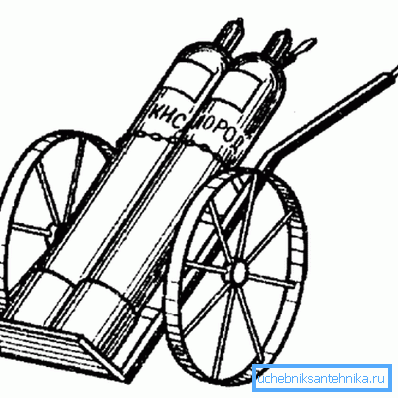
- During work on the loading of cylinders it is worth removing any jewelry, first of all - wedding rings. The demand may seem comical, however, it has suffered from the experience of many welders who have lost their fingers because of the ring hooked on the valve.
- Any works with electric welding are carried out on a dry floor. On a metal base must use rubber mats.
- Plumbing before welding work is not only turned off, but also discarded. Boiling water can cause serious burns as well as electric shock when hit on the mitten and holder.
Plastic
How is butt welding of polyethylene pipes and products made of polypropylene? Oh, with the work on steel, it has nothing to do. The essence of the method is in the melting of the joined ends and their combination with a small clamp.
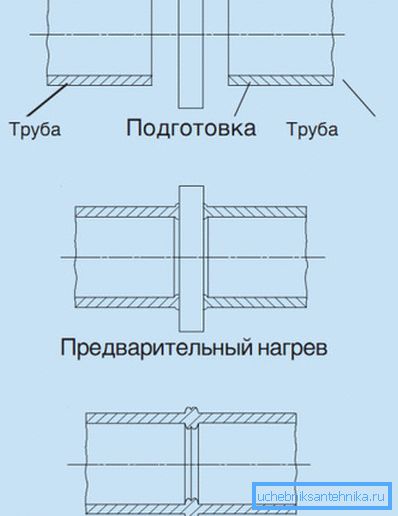
Further work will be performed by molecular diffusion - you just need not to touch the joint for a while.
And what about coupling connections? The principle is similar; the only difference is that not the ends of the pipes being joined are welded, but the pre-melted outer surface of the pipe and the inner one - the couplings.
When is butt welding used, and when are couplings used?
It's simple: in order to butt the plastic pipe, its diameter should be equal to or greater than 50 mm, and the wall thickness should be at least 4 mm.
Equipment
The simplest butt apparatus for welding polyethylene pipes is the so-called mirror, a heating element in the form of a flat pancake. Often, universal soldering irons are used in this capacity, which allow making coupling joints: their flat heater is supplied with nozzles for pipes and fittings of different diameters.
Important: since such equipment does not provide accurate centering, butt welding of polyethylene pipes on hand-held soldering irons is permissible only for low pressure pipelines (summer water pipelines, self-flowing sewers of small diameter).
More serious welding machines allow mechanical centering and clamping of pipes. With a pipeline diameter of 250 millimeters, hydraulics must come to the rescue: since both the diameter and wall thickness are large enough, to ensure accurate alignment and clamping without its help is very problematic.
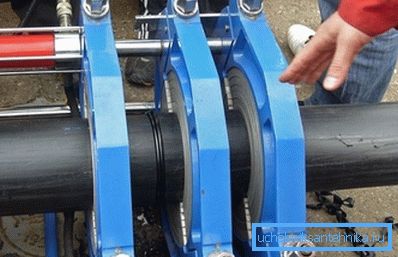
Technology
What is the technology of butt-welding of polyethylene pipes with a large (over 150–200 mm) pipe diameter?
- The pipes are mounted in ring clips and centered.
- Their ends are trimmed with a mechanical facer.
- The alignment and the size of the gap is checked.
- The heating element heats the ends, after which it is removed from the heating zone.
- Pipes are joined under pressure. The clamping force is about 1.5 kgf / cm2.
- After cooling, the melt (melt extruded at the seam) is removed; the interface is ground.
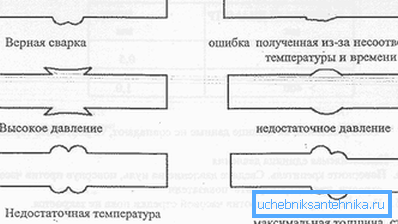
The temperature of the heating element and the heating time is determined by the wall thickness of the welded pipes. Here is the rate of welding of joints of pipes made of polyethylene for the entire range of values of thickness.
Wall thickness mm | Mirror temperature, С | Duration of heating, s |
4.5 and less | 210 | 45 |
4.5 - 7.0 | 207 | 45 - 70 |
7.0 - 12.0 | 200 | 70 - 120 |
12.0 - 19.0 | 197 | 120 - 190 |
19.0 - 26.0 | 193 | 190 - 260 |
26.0 - 37.0 | 192 | 260 - 370 |
37.0 - 50.0 | 191 | 370 - 500 |
50.0 - 70.0 | 190 | 500 - 700 |
Of course, a number of subtleties exist here.
- The base on which the welding is performed must be rigid and precluding displacement when the seam solidifies. On wooden grounds used wooden shields.
- The maximum axial displacement should not exceed 1/10 of the wall thickness.
- In windy weather, the back ends of the pipes are silenced in order to avoid drafts that can lead to uneven heating of the seam.
- Before fixing, the ends of the pipes should be wiped with a lint-free cloth.
- The marking of the connected pipeline sections when they are fixed in the chassis should be in one line and look into the upper hemisphere.

What does butt welding of HDPE pipes look like when using hand tools?
The principle is the same:
- The ends of the connected pipes end strictly at right angles to the longitudinal axis.
- They simultaneously and strictly at right angles are pressed against the mirror warmed to 220 ° C for 20-30 seconds.
- Then the ends with force pressed against each other and held in this position for 40-60 seconds.
- The brat is removed after complete cooling with a sharp knife.
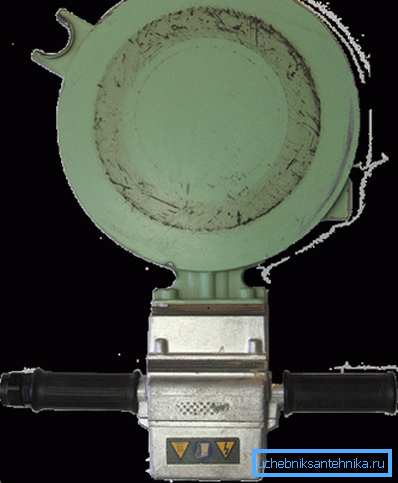
Rates
How much does it cost to weld a PND pipe joint using industrial equipment?
The price predictably depends on the diameter of the pipeline. We give a quote from one of the Moscow companies.
Diameter, mm | The cost of one joint, rub |
63 | 200 |
75 | 250 |
90 | 300 |
110 | 400 |
125 | 600 |
140 | 650 |
160 | 900 |
200 | 1100 |
250 | 1700 |
315 | 2200 |
400 | 3300 |
450 | 3900 |
500 | 4900 |
630 | 5800 |
800 | 8600 |
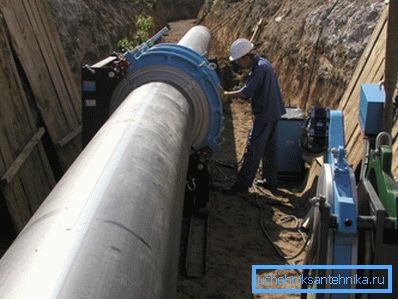
Conclusion
As already mentioned, the material offered to the reader does not claim to cover all possible technologies and solutions. This is just an attempt by the author to share his modest experience and knowledge (read also the article Viniplast tube - features and scope).
As usual, additional information can be found in the attached video in this article. Successes!