Copper pipes for heating: application features and basic
According to statistics, copper pipes for heating and water supply are much less common than steel and polymer counterparts. Meanwhile, experts are unanimous about the fact that copper is the best material for plumbing.
What then explains the fact that products made from this non-ferrous metal are used infrequently? The reason is obvious - the cost of installation, as well as the cost of the finished pipeline is high and not affordable for everyone.
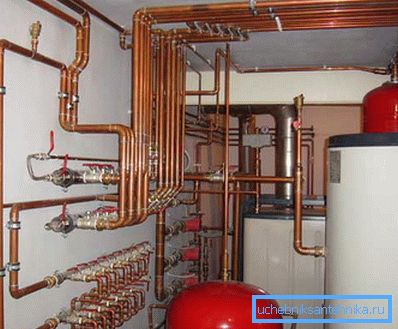
So why the installation of heating from copper pipes is expensive and what are the advantages of such systems?
Classification
Modern heating with copper pipes requires the need for professional installation and proper selection of all structural elements that may be involved in the assembly of the system. For ease of selection of parts required for the assembly of the heating system, a special classification has been developed.
Copper pipes, according to standard sizes, are classified on the following modifications:
- Thick-walled products with a wall thickness of up to 1.5 mm are used for arranging heating systems in individual housing construction objects.. The production of such products is carried out in accordance with GOST 617 - 90. In the manufacture of these pipes, such copper grades as M1, M2 and M3 are used.
- Thin-walled products differ from thick-walled analogs only in wall thickness, in this case it does not exceed 0.7 mm.. Such products are used in autonomous systems of heating in small rooms where it is possible to set low parameters of heat carrier pressure.
Important: The price of pipes is largely determined by the grade of metal used, but in this case the mark does not indicate special performance, but rather indicates the content of impurities in the alloy. Therefore, to overpay for the brand does not make much sense.
In accordance with the method of manufacture, the pipes are divided into:
- pulled modifications - denoted by the index "C" and are made of welded blanks;
- cold rolled modifications are denoted by the āDā index.
Also, when choosing copper pipes for the manufacture of heating systems, it is necessary to take into account that modifications from more ductile and, as a result, simple alloys in processing, and modifications from more rigid alloys are on the market.
Advantages and disadvantages
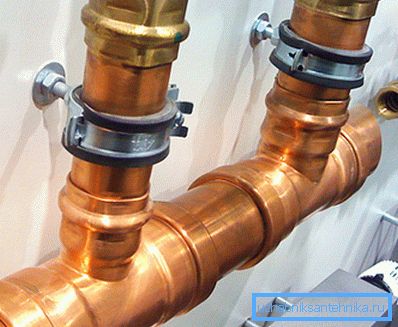
As already mentioned, the cost of copper pipes for heating is high and this is probably their only drawback. On the other hand, is it really a disadvantage that the heating system you have acquired will be prestigious and exclusive?
Along with the high cost, there are many advantages, among which we note the following:
- excellent appearance;
- absolute resistance to corrosive processes (copper, when oxidized, does not rust, but is broken by a noble patina, which makes it even more attractive);
- high thermal conductivity and, as a result, better heat transfer to the heated room;
- environmental safety, since such a metal, when heated, does not release toxins and allergens into the environment;
- resistance to the negative effects of chlorinated water and reagents dissolved in the heating medium of centralized heating;
- despite the complexity of the installation work, there is an opportunity to do it yourself;
- long service life of the system up to one hundred years, provided proper installation.
Features of the installation work
The installation of copper heating pipes is largely determined by the type of fittings used.
The greatest relevance use fittings for compression (crimp) connections for threaded connections and for soldering.
Important: Regardless of the installation method you choose, you should make sure that the pipe fittings used are also copper. If pipes and fittings are made of different metals, this will cause a series of electrochemical reactions that will weaken the integrity of the pipeline.
- The compression joint is made using special crimping pliers, with which the fitting is pressed to the pipe along the entire radius. Despite the seeming simplicity of the process, heating from copper pipes with their own hands can be collected only with a special tool.
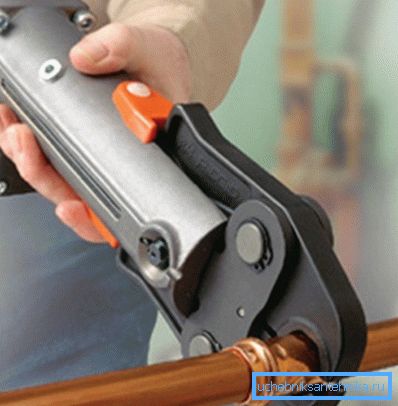
Prior to crimping, the edge of the pipe is cleaned with scotch light and wiped with a solvent. Next fitting worn on the seat and crimped.
The connection is strong and durable, but disposable. Therefore, before fixing the connecting elements on the pipes, everything should be carefully measured.
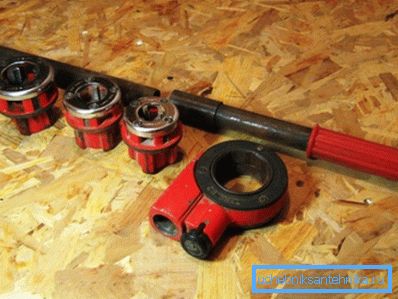
- The threaded connection is much more difficult to make than crimping, since you will have to cut the thread.
Important: It is advisable to perform thread cutting on thick-walled copper pipes, since thin walls can be crushed or cut with insufficient installation experience.
Threading is done with dies for pipes - a special device with handles and cutters. In modern sets, special inserts are used, selected in accordance with the thread pitch and pipe diameter.
The principle of using the tool is the following: we apply engine oil on the metal, set the tool and scroll forward a couple of turns forward and vice versa back. Then again we make a few turns forward and one turn back.
Threaded fittings are screwed onto threaded threads using fum-tape. Some fittings provide for a rubber sealing ring and in this case no fum tape is needed.
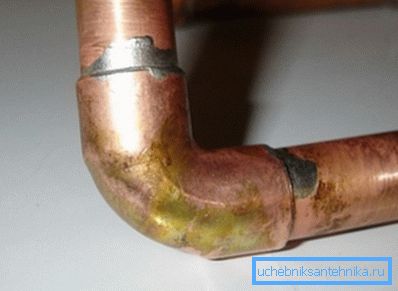
- Brazing copper heating pipes is the most effective, but at the same time, time-consuming method.. Tools such as a gas burner, pipe cutter, countersinker and Scotch Bright are required. From materials other than pipes and fittings, you will need solder or flux.
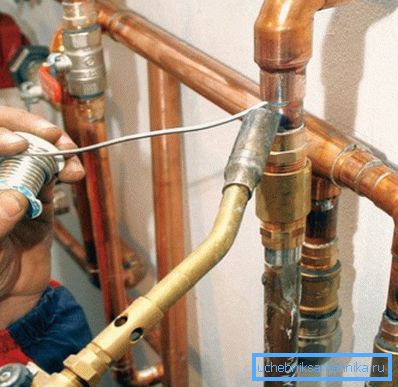
- Cut the pipe and chamfer along the edge.
- We clean the edge of the Scotch Bright to shine and do the same with the internal volume of the fitting.
- Apply solder to the seat and put on the fitting pipe.
- We heat the place of soldering with a gas torch until the solder appears outside.
- While the metal is hot, remove the excess solder with rags.
Conclusion
Now you know what are copper pipes for heating and how to assemble a single hermetic system from them. Have any questions? More useful information you can find by watching the video in this article.