Cross-linked polyethylene pipes and fittings: technical
Not so long ago, the main material for the manufacture of water supply, drainage and heating systems were metal pipes connected by gas welding. But now they are being replaced by parts from various polymers, which have many advantages. The most common polyethylene pipes and fittings for water supply.
Let us consider in more detail their technical characteristics and consumer properties.
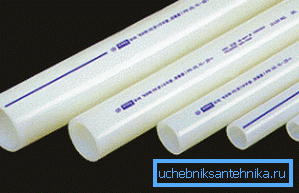
Features of polymer parts
The production process of elements of cross-linked polyethylene
In the manufacture of pipes from this type of plastic, not separate layers or sheets are to be “stitched”, as unknowing masters might think, but individual molecules.
In the process of creating the polymeric form of ethylene, its molecules receive additional cross-links, which make it possible to form a kind of three-dimensional network. Thanks to her, the material acquires enhanced technical characteristics.
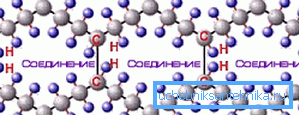
"Stitching" is made by chemical or physical effects.
Depending on the method of production of pipes from polyethylene (marked PE-X), the following types of material are distinguished:
- PE-Xa - made by heating with the use of peroxides;
- PE-Xb - polyethylene, which is treated with a special liquid containing silane (silicon compound with hydrogen) and a special catalyst;
- RE-Xc - the material is obtained after the bombardment of polyethylene molecules by electrons in a special device;
- PE-Xd - in the manufacturing process of this material is used nitrogen.
Tip! For the arrangement of domestic water supply systems, the material obtained by the peroxide method and labeled with PE-X is best suited. It is distinguished by its low price and ease of installation. All work can be done by hand.
Technical characteristics of pipes
Details for plumbing and heating of cross-linked polyethylene have many advantages:
- Long service life. The operation time of the plumbing or heating of these parts at the limiting temperatures of the coolant (up to 95 degrees Celsius) is from 15 to 50 years.
- Geometric stability. Even in the case when the liquid is transported through the pipes at a temperature of 200 degrees Celsius, the material retains its original shape (in the absence of additional external influence).
- Products are resistant to cracking during installation and operation.
- The material does not collapse during impacts and in the process of cutting, even at an ambient temperature of 50 degrees Celsius.
- Products made of cross-linked polyethylene have an optimal ratio of price and quality.
- They have enhanced abrasion resistance, are excellent for installing underfloor heating systems with heat-transfer fluid.
- Material does not shrink after installation.
- Pipes of cross-linked polyethylene are not susceptible to corrosion and do not require additional measures of protection (painting and the like).
- Resistant to the effects of various chemicals.
- The material does not contain halogen ions and heavy metal molecules, which adversely affect human health.
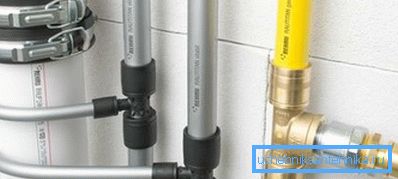
Note! In the process of "stitching" of polyethylene, its crystal structure changes, so the material becomes more elastic and does not break at the bends, including at negative ambient temperatures.
Types of connecting elements
Fittings for cross-linked polyethylene pipes are used to connect individual elements into a single system.
These fittings can be made from a variety of different materials:
- polyethylene;
- polypropylene;
- polyvinyl chloride;
- combined.
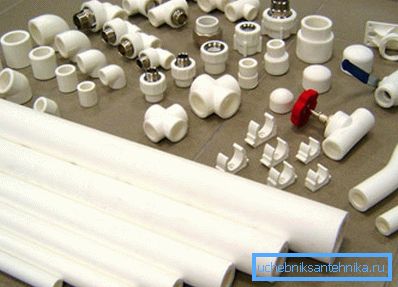
Depending on the method of installation share:
- compression fittings for polyethylene pipes - use crimp nut, screwed onto the main part of the part with a wrench;
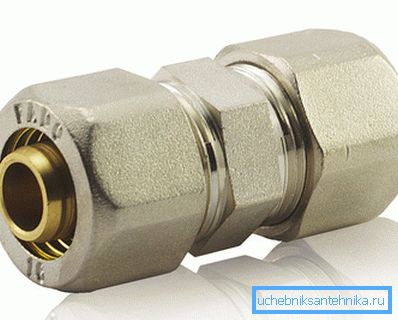
- clamp fittings for polyethylene pipes - a special one-piece sleeve is used, which is pressed on the choke using a press;
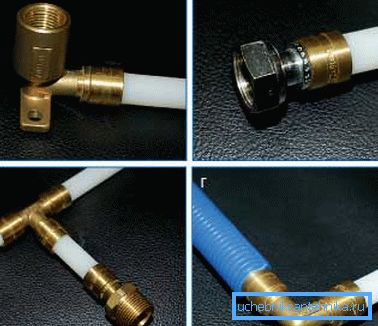
- electrofusion fittings for polyethylene pipes - for the connection, a built-in heater is used, heated with a special apparatus, which fuses the inner surface of the nozzle and seals the connection.
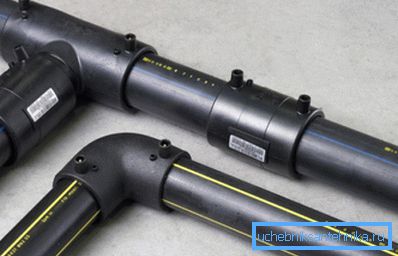
There are the following constructions:
- Cap - is used to seal the dead-end design element.
- Coupling - is used to connect two components of a water supply or heating system.
- Squares - necessary for the angular connection of segments and changing the direction of laying the network.
- Pipe tees - with their help, three different parts are joined in one knot.
- Cross fittings - used for arranging the wiring of the pipeline system, in this case, four pipes are connected at the same point.
- Driving is necessary in order to attach new elements to the already existing system.
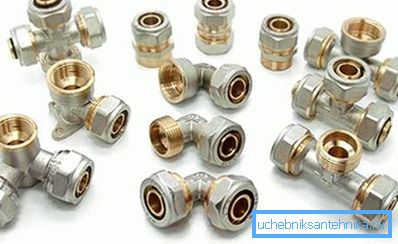
Note! The design of the fittings may vary depending on the manufacturer. It is possible that the joining parts do not fit the pipes. Keep this in mind when shopping.
System installation
Instructions for the manufacture of plumbing and other similar systems differs depending on the fittings which design you want to use.
Compression
This method of connection is simpler and can be used for the installation of pipes of both cold and hot water supply. You do not need to use any special tool, just take two ordinary wrenches, as well as scissors for cutting.
Fittings are installed as follows:
- A fitting nut is put on the end of the part. The threaded part must be directed towards the cut-off side.
- Then a split ring is installed on the part. Its edge should be at a distance of 1 mm from the cut.
- A fitting is inserted into the pipe from the fitting. Before this, it is not necessary to carry out any manipulations with the part (for example, chamfering).
- After that, the nut is tightened on the fitting using a wrench. It does not need to make too much effort, as there is the possibility of damage to the polyethylene.
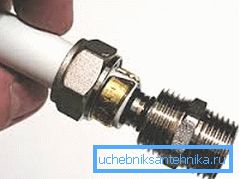
Press fittings
These fittings are also reliable and tight, but the result is a permanent connection. In addition, for crimping the liner will require the use of special tools.
The installation process is as follows:
- A disposable sleeve is put on the end of the part, with which the fitting will be fixed.
- An extender of the required diameter is inserted into the end of the polyethylene part. It must be placed all the way on the handle and left for a few seconds.
- Then pull out the expander and insert the fitting. The peculiarity of cross-linked polyethylene is that the material has a molecular memory. After some time, the product will reverse shrinkage, which will provide additional tightness.
- After that, the sleeve slides on the end face and is pressed there using a special tool.
Unlike conventional polyethylene pipes, which have a strong coefficient of linear expansion, "stitched" parts are almost devoid of this drawback. Therefore, they are recommended to be used for arranging hot water systems.
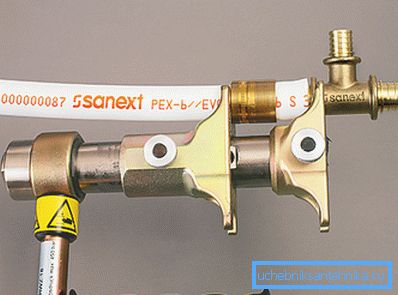
Conclusion
Cross-linked polyethylene is an excellent material for the installation of plumbing and heating systems (see also the article Chrysotile Cement Tubes: Properties and Applications).
More details about this can be found in the video in this article.