Electrofusion pipe welding
Laying of the pipeline or main sewage system cannot be done with a single piece of material. To date, many methods have been developed by which the connection of individual segments is made. The most advanced is the electrofusion pipe welding.
What is it
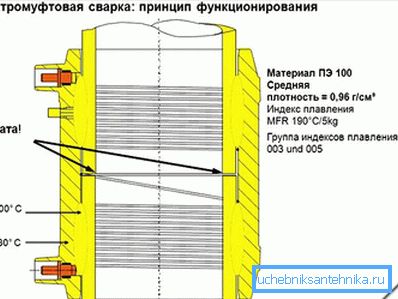
The essence of the method lies in the fact that the connecting fitting has an electrical spiral in it. It can be fully open, partially buried or hidden. The heating element has two outgoing contacts to which the welding machine is connected. The specified value of the voltage is supplied for a specified period of time. The inner part of the connector and the inserted section of pipe under the action of temperature becomes liquid. The outer wall does not heat up to such an extent and retains its elasticity, which causes the substance to move downwards, as a result of which a monolithic structure is formed.
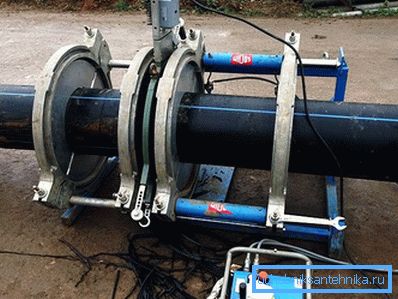
Couplings are made of three types of plastic: polyethylene, polypropylene, polybutene. For the installation of gas lines are usually used only the first option.
Tip! Marking is applied to the fittings, which informs the operator about what voltage and for what period to apply. Also indicates the cooling time of the finished joint. Additionally, the design provides for special indicators that signal the completed process.
Benefits
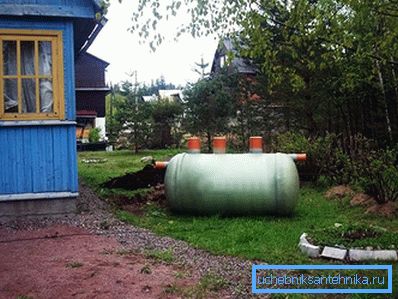
This technological method has many positive aspects:
- During welding, the internal diameter of the pipe does not decrease. This means that it can be used not only in cases where the system has a pressure head with constant pressure. Drainage and storm systems are no exception.
- Thanks to a well-thought-out instrumental base, the human factor is reduced to a minimum when performing all the required operations.
- This method is more acceptable if you need to adhere two large-diameter pipes.
- Electrofusion welding will be indispensable when repairing the main line is required, and it is not possible to displace the pipes in the horizontal plane.
- An obstacle to articulation will also not be the case when both or one of the pipes is reinforced with reinforcing inclusions. When butt welding there is no guarantee of such strength of the seam.
- Pipes from the sewed polyethylene usually connect mechanically. ZN welding provides an opportunity to affect molecular bonds, providing a high-quality seam.
- The assembly of a pipeline with a plurality of taps can be carried out directly at the site, without the need for preliminary connection and installation of a ready-made structure.
- Saving electrical energy compared to other types.
- The advantage of welding products from different grades of polyethylene, as well as different diameters.
Tools
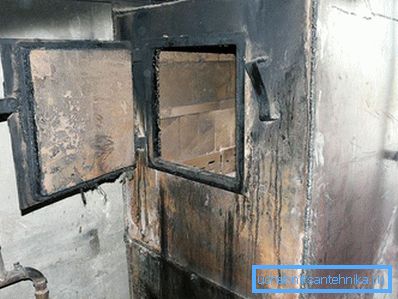
In order for the whole process to go smoothly, you need to have a specific tool with you:
- Welding machine. A unique unit was developed for this type of welding. It is based on semiconductor technology, so it consumes an order of magnitude less electricity than its other counterparts. Usually for such units the maximum and minimum welded diameters are indicated. There is a barcode scanner that automatically enters data about a specific type of connection, it can also be done manually. The data on each passed joint is stored in memory so that the operator or control group can get information. You may have a built-in serial or USB port, you can connect a flash drive to the latter to transfer settings or data. The front panel usually has a display that displays the current settings. Complete with some units are tips of various sections.
- Positioner Small metal fixture in the form of a strip that has several clips. This tool allows you to position the pipes in the same plane for welding. It is also intended to correct ovality. For these purposes a separate clamp can also be used.
- Truborez. Usually use disk. It is he who makes it possible to perform an even cut, which is a requirement.
- Scraper. Small handle with a blade. It can also be a fixture with several modules. One of them is placed in the pipe, the second, on which the cutting head is located, connects and removes the upper layer during rotation. This procedure is necessary not to create a rough surface, but to remove the oxidized part of the nozzle.
- Roulette or ruler.
- Cleaner. It is necessary to remove dirt and grease. It should be used specially designed for a specific type of pipe. Do not use ordinary alcohol or acetone.
- Marker. A waterproof white or bright color is used to apply not only the markings, but also some data in place of the spikes.
Tip! For the saddle insert, a special drill is also used, as well as a hexagonal key and a screwdriver for the latches.
Installation
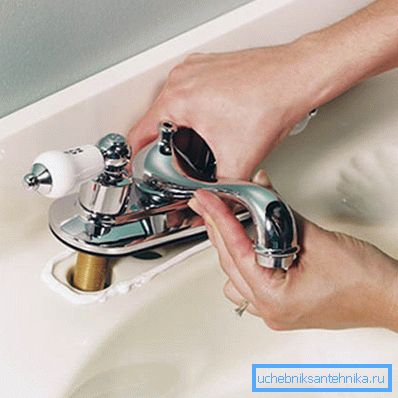
The spike process is not very complicated, but it requires a certain accuracy, attention and perseverance.
- If there is time before work, it is advisable to straighten the pipe in 24 hours, unwinding it from the bay, this will help to partially correct the ovality.
- The first thing to do is trim the edge of the pipe. For these purposes it is possible, but not desirable, to use a hacksaw. The butt is rough. Use a disk pipe cutter, it will provide the correct plane.
- Next is the markup. It is necessary to apply the line to which the fitting will be worn. From her make a margin of another 1-2 cm and mark.
- Using a scraper or mechanical oxide cleaner, remove the top layer. For pipes whose diameter does not exceed 63 mm, it is 0.1 mm. If the outer diameter is larger, then you need to remove 0.2 mm.
- Now the pipe is treated with solvent and placed in the positioner. It must be well fixed and correct ovality. The fitting should not be subjected to fracture stress. The positioner must compensate for it.
- The coupling is put on (it must also be treated with a solution from the inside). If the diameter of the pipe is very large, then the coupling is stretched to its full size. The second branch pipe is brought in and the fitting is knocked down to half its depth. Mortgage helix must be in its entire pipe area to ensure proper alloying.
- After connecting two pipes, the welding machine is connected. The necessary parameters are read by the scanner or entered manually. The process starts. It is important to remember that the cooling time also includes a full cycle. If the clip is removed before time, the tightness will be broken.
- When all tasks are completed, the time and date, as well as the operator, are put on the connection.
- Mounting a saddle insert has a similar algorithm. Cleaning is performed at the place of installation, but not around the entire circumference, but only the area of the adhesion, which will be blocked by a spiral. After stripping, the saddle is put on and firmly clamped. Welding is performed. Further, with the help of an additional tool, a cut is performed. With the help of a plug the technological opening is closed and a label is applied.
Tip! To remove the oxide, do not use sandpaper or inappropriate scrubbers. You will simply scratch the surface, but you will not achieve the desired result.
Typical mistakes
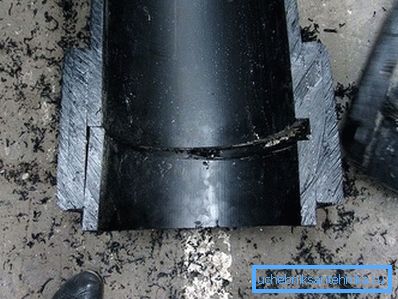
In some cases, the connection is depressurized. This can be detected already at the completion of a complete installation. This happens for the following reasons:
- The operator did not compensate for ovality. This may cause the molten plastic to not fill the entire space.
- Scraping was not done with a scraper. The result will be that the coupling and the pipe do not form a monolithic soldering.
- The pipe was at an angle to the fitting. The consequence will be the leakage of liquid plastic.
- The fitting was not fully fitted. Mortgage helix will not melt a sufficient amount of articulated surface.
- No degreasing was performed or after it was touched to the place of cleaning. Connection will not be tight.
For the connection of HDPE pipes this instruction is also applicable. This method is much better than using fittings with a mechanical clamp that cannot provide perfect tightness.
Video
The provided video materials show the technological process of electrofusion pipe welding: