Fiberglass pipes: advantages, production technology,
What is the production of pipes made of fiberglass? What should be fiberglass pipes according to GOST? How attractive are their characteristics against alternative solutions? Let's try to answer these questions.
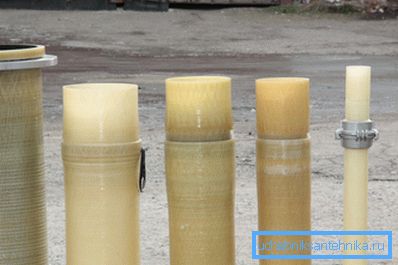
What it is
What is fiberglass? The name, in general, gives a comprehensive picture of the composition of the material: the binder (epoxy or polyester resin) is reinforced with fiberglass. Reinforcement provides resistance to tensile and flexural loads; Binder ensures resistance to shock loads.
Please note: resins used are typical thermosets. When hardening, irreversible chemical changes occur in them; if so - unlike thermoplastics, resistance welding of products is impossible. Glue, flanges for bolts, threads, etc. are used to connect pipes.
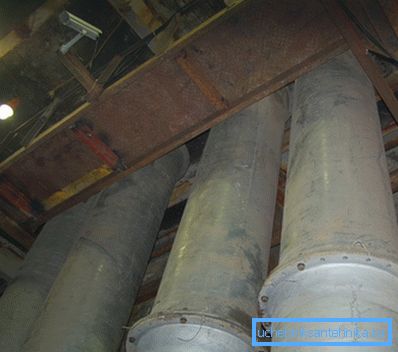
Story
The production technology originated in the fifties of the last century, when industrial production of epoxy resins began. Like any new technology, at the initial stage this was not very popular: the lack of experience in using fiberglass supplemented the low price of traditional materials (steel, copper and aluminum).
Around the mid-60s, however, the picture began to change.
What happened?
- Steel and nonferrous metal prices rose.
- Commercial development of offshore oil and gas fields has begun. GRP tubing (tubing) favorably differed from metal by low weight and, more importantly, corrosion resistance: contact with salt water did not cause them any damage, unlike competing products.
- Finally, the fiberglass production technologies themselves also did not stand still: it became cheaper and more durable.
The result was not long in coming: by the end of the 60s, the American company Ameron entered with its high-pressure fiberglass pipes first into the North American and then into the Middle Eastern market. By the 80s, European and, a little later, Soviet (later - Russian) manufacturers were brought up.
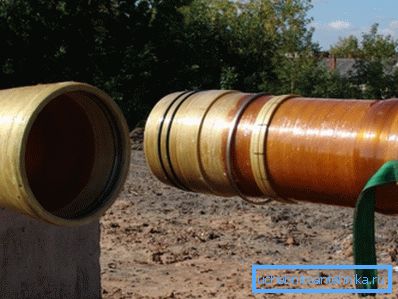
Benefits
Than fiberglass has gained popularity?
The list of its advantages is not too large, but it looks very convincing.
- Very reasonable against the background of high-alloyed and stainless steels cost.
- Resistance to corrosion and aggressive media.
It is useful: if it is necessary to transport especially aggressive liquids, the pipeline elements are lined with high-pressure polyethylene.
- Low weight. The specific strength of fiberglass (strength related to density) is 3.5 times higher than that of steel; Thus, equal-strength structures of these materials will differ in weight several times.
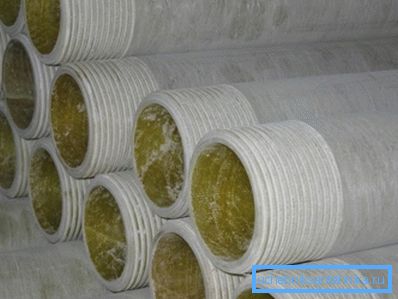
- The possibility of obtaining material with desired mechanical properties due to a specific reinforcement scheme. For example, the spiral-ring winding of fiberglass provides the highest resistance to internal pressure.
Production
What is the production of fiberglass pipes?
To date, there are four main technologies of their manufacture.
Title | Description |
Extrusion | The resin is mixed with a hardener and chopped fiberglass, after which it is extruded through an annular hole. Production is cheap, technologically, but the lack of a regular reinforcing frame affects the final strength of the products. |
Pultrusion | The tube is formed between the inner and outer mandrels. Both surfaces are perfect; However, a number of technological limitations do not allow producing pipes of large diameters and with high working pressure. |
Centrifugal molding | Reinforcement is a finished sleeve of fiberglass, which is pressed against the surface of a rotating form by centrifugal forces. They also contribute to a uniform distribution of resin in the future walls. The main advantage of the technology is the ability to get a smooth outer surface; the main drawback is energy intensity and, accordingly, high cost. |
Winding | Fiber-impregnated glass fiber (thread, tape or fabric) is wound on a cylindrical mandrel. Equipment for the production of fiberglass pipes by the winding method is most common due to the relative simplicity and high performance. |
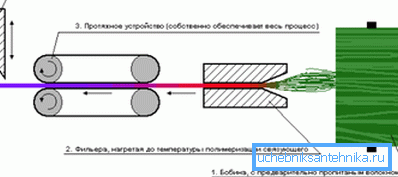
The latter method of production has several, so to speak, subspecies. Let's get to know them.
Spiral ring winding
The stacker — a ring with several impregnated thread feeding mechanisms — reciprocates along a rotating mandrel. At each pass, a layer of fibers with a constant pitch is laid; ring scheme of laying, as we remember, allows you to achieve maximum pipe strength at break.
Curiously, the pre-tension of the thread also favorably affects the final strength of the product, preventing the occurrence of cracks under bending loads.
Spiral-ring winding method is used to manufacture tubing pipes designed for high operating pressures, structural components (including composite power transmission tower supports), and even the hulls of rocket engines.
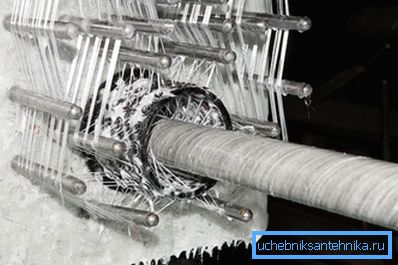
Spiral tape winding
The difference with the previous method is only in the fact that in one pass the stacker forms a narrow ribbon of a dozen or two fibers. Accordingly, for the formation of continuous reinforcement requires much more passages; the reinforcement itself is somewhat less dense. The main advantage of the method is much simpler and, accordingly, cheap equipment.
Longitudinal transverse winding
The principal difference from the previous schemes is that the winding is made continuous: the stacker simultaneously lays down the longitudinal and transverse threads. It would seem that this should simplify and cheapen the technology; however, there is a purely mechanical problem.
The mandrel on which the future tube is wound rotates; if so, then the coils from which the thread of longitudinal reinforcement is unwound must also rotate. Moreover, the larger the diameter of the pipe, the greater must be the coils.
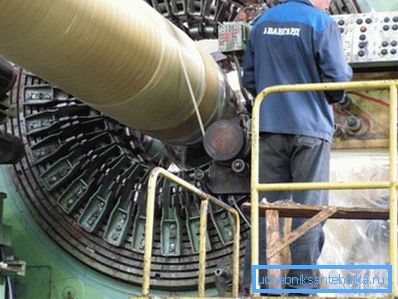
Oblique transverse longitudinal winding
This solution was developed during the life of the Soviet Union in Kharkov and was initially used in the production of rockets shells. Later it became widespread throughout the post-Soviet space.
What is the essence of the method?
- The stacker forms a wide ribbon of parallel binder-impregnated fibers.
- The tape before winding on the mandrel is pre-wrapped with a thread without impregnation, subsequently forming an axial reinforcement. The threads collected in the tape themselves form, respectively, transverse reinforcement: the tape is laid across the mandrel axis.
- After laying each layer is rolled rollers, sealing reinforcement and displacing excess binder.
What is the advantage of such a scheme?
- The possibility of continuous production. In one pass, you can form arbitrarily thick walls, simply changing the overlap of the tape.
- High performance.
- The ability to produce fiberglass pipes of large diameter (in theory - without any restrictions of the maximum size). Dimensions are limited only by the size of the mandrel.
- Extremely high fiberglass content in the finished material. It comes to 85% against 45-65% with alternative methods. This affects both the final strength and the flammability of the product.
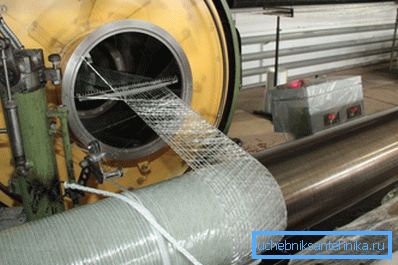
Standards
Production of products of interest to us is regulated by two regulatory documents:
- GOST R 53201-2008 contains technical conditions for the manufacture of pipes with a diameter of 50-200 mm on threaded connections.
- Developed with the participation of NTT LLC (New Pipe Technologies), GOST R 54560-2011 describes the details of glass fiber reinforced thermoset plastics.
We study the basic provisions of the documents.
GOST R 53201-2008
The standard pipe operation mode is as follows:
- Temperature - from -60 to + 60C.
- Relative humidity - up to 100%.
- The temperature of the transported liquid is up to + 110 ° C.
- Working pressure - from 3.5 to 27.6 MPa.
The following uses are provided for the products described by the standard:
- Transportation of oil and gas condensate.
- Transportation of salt solutions (including sea water).
- The construction of lift columns.
- Fastening wells for various purposes.
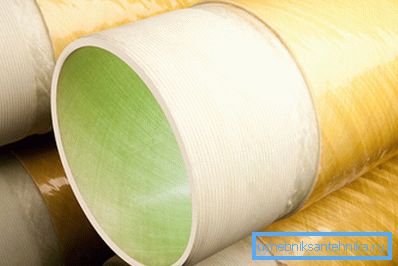
- Maintaining reservoir pressure in the development of underground deposits.
- Technical and drinking water supply.
The standard distinguishes three types of pipes:
Designation | Decryption |
NK | Pump-compressor |
ABOUT | Upsetting |
L | Linear |
What can be the diameters of fiberglass pipes produced according to GOST R 53201-2008 and their other characteristics?
Pumping and casing
Internal diameter, mm | Nominal pressure, MPa | Minimum wall thickness, mm | Weight per meter, kg |
50 | 6.9 - 27.6 | 4.3 - 8.4 | 1.6 - 3.3 |
63 | 6.9 - 27.6 | 4.6 - 10.7 | 2.2 - 5.5 |
100 | 10.3 - 17.2 | 8.1 - 12.2 | 5.8 - 8.2 |
150 | 10.3 - 17.2 | 13.5 - 15.0 | 14.0 - 14.9 |
200 | 10.3 | 13.6 | 16.5 |
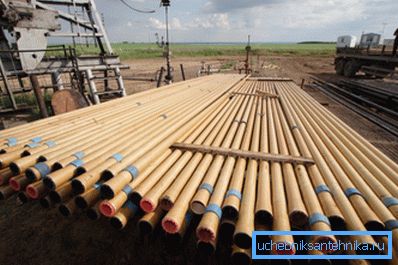
Linear
Internal diameter, mm | Nominal pressure, MPa | Minimum wall thickness, mm | Weight per meter, kg |
50 | 10.3 - 27.6 | 2.79 - 8.10 | 1.2 - 3.1 |
63 | 8.6 - 27.6 | 2.80 - 9.90 | 1.4 - 5.2 |
100 | 5.5 - 27.6 | 2.80 - 16.00 | 2.3 - 12.8 |
150 | 5.5 - 13.8 | 4.57 - 11.20 | 5.1 - 12.2 |
200 | 5.5 - 13.8 | 5.84 - 14.70 | 8.6 - 22.6 |
In addition to pipe sizes, the document contains detailed instructions for the manufacture of fittings with an indication of basic dimensions, requirements for appearance, maximum tolerances and labeling of all products.
GOST R 54560-2011
The standard describes pipelines that are operated in much milder than the conditions described above:
- Operating pressure - up to 3.2 MPa;
- Medium temperature - up to 35 ° C;
- Transported liquids - water, water solutions and drains (domestic and industrial).
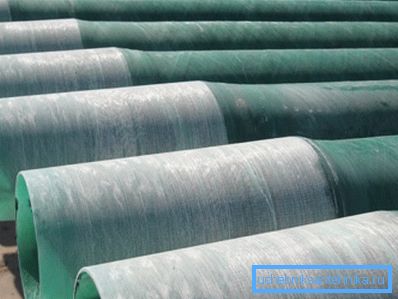
Important: the action of GOST does not apply to pipelines for domestic water supply and sewage.
Within the framework of the document, products are classified according to the following criteria:
- Diameter (DN). The range of values is from 300 to 3000 millimeters.
- Nominal pressure (PN). For non-pressure pipes, the concept of PN itself is rather arbitrary and is taken to be 0.1 - 0.4 MPa; for pressure, it takes values of 0.6, 1.0, 1.6, 2.0, 2.5 and 3.2 MPa.
- Rated stiffness (SN). It is also measured in megapascals and can be equal to 1250, 2500, 5000 and 10000.
Please note: when laying a fiberglass sewage system with your own hands, it should be borne in mind that SN 1250 pipes are not recommended for underground installation in principle, and SN 2500 is recommended to be laid in trays.
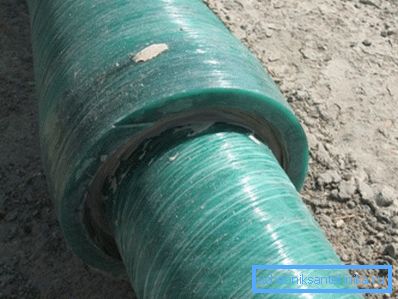
The document, like the previous one, lists the main dimensions of all types of fittings and requirements for their appearance, strength, marking and methods of reinforcement.
Conclusion
Of course, in our material we touched only a small part of a very extensive topic of using fiberglass. We have not figured out whether it is possible to use fiberglass pipes for heating or domestic sewage, how good they are on the background of metal-polymer or all-plastic products. Some of these questions affect the video in this article. Successes!