Fittings for metal pipes: connect parts in different ways
Fittings for metal-polymer pipes, as well as parts for assembling communications made only from metal elements, can be very different. In this case, the differences lie in the material from which the connectors are made, and in their design.
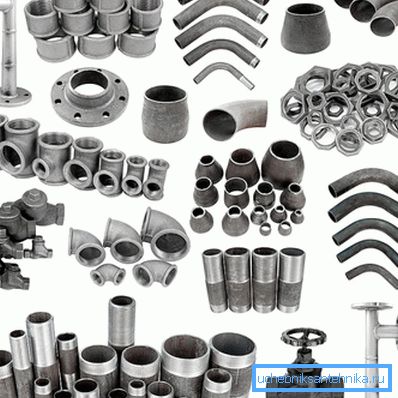
Below we look at the main types of parts, paying attention to their strengths and weaknesses.
What are they made of?
An overview of the range of fittings will begin with an analysis of the materials used to produce them. As a rule, the metal connecting part coincides with the metal used for the laying of pipe communications, but there are exceptions.
Most often for the manufacture of pipe connectors are used:
- Cast iron. The material is resistant to stresses and chemical influences, withstands high pressure. Most cast iron models provide a threaded connection, but you can also find couplings that require additional sealing with cement mortar, sealants, or even lead. The disadvantage of cast-iron fittings is a large mass and high price.
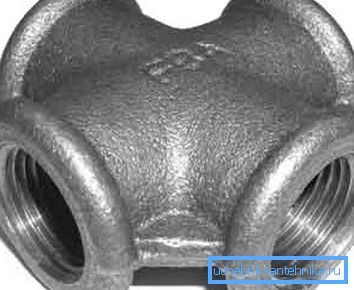
- Steel. It is used in the same place as cast iron, which is less brittle due to greater elasticity. Unlike cast iron, steel fittings fail earlier because they are more susceptible to corrosion (including electrochemical).
- Brass. A good option in terms of connection reliability, durability and performance. Brass fittings can be used for arranging metal pipelines, as well as when installing plastic communications.
- Copper. Such parts will be the most expensive, but at the same time they provide the most reliable and durable connection of pipes. Most often used in heating systems, but may be involved in the assembly of water pipes in private homes and commercial organizations.
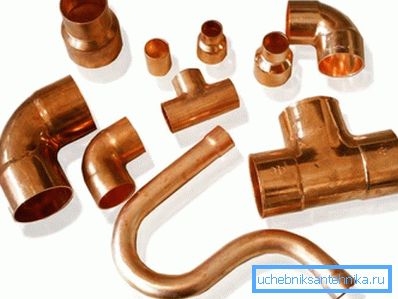
Note! Copper and brass are rarely used for the laying of trunk communications.
In addition, when arranging water supply systems based on metal-plastic pipes, also connectors made of technopolymers with metal (steel or brass) inserts are used.
Varieties of design
For welding or brazing
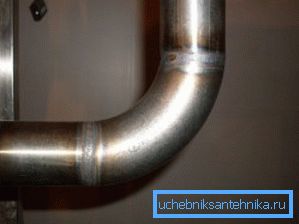
If the materials are more or less clear, try to understand the configurations.
The simplest are connectors for which welding is used or (in the case of copper / brass parts) soldering.
- The welded fitting represents a fragment of a pipe of a certain configuration. As a rule, its diameter corresponds to the diameter of the connected pipelines, which allows welding the edges of the products end-to-end.
- The absolute majority of welded fittings are made from “black” steel. In this case, the weld is obtained sufficiently reliable to withstand the highest possible pressure.
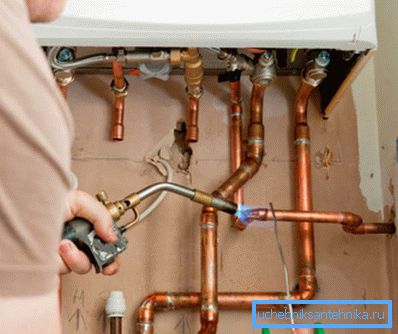
- Copper and brass parts are produced for which soldering is applied. Their configuration provides for the presence of a socket for the installation of the pipe, while the minimum gap for filling with solder must remain.
Note! Welding and soldering pipes are quite complex technologies that require long-term development. So the text instructions and explanatory videos should be studied thoroughly, and best of all - under the guidance of an experienced master.
Under the thread
Threaded parts are among the most common. They can be made from any of the above material, but the primacy in this segment surely hold steel and brass.
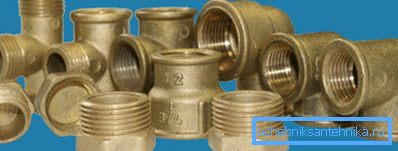
The following is typical for threaded connections:
- Most often, such parts are used for joining pipes with a diameter of 50 mm or less. With a longer circumference, the thread cannot provide the required tightness.
- For arranging a knee, tee or crosspiece, it is necessary to have a thread not only on the fitting, but also on the pipe. In some cases, cutting must be done independently with the help of special tools - dies.
- Sometimes connections require additional compaction. To this end, a coil of synthetic (polymer tape) or natural (flax tow and analogs) material is made at the junction.
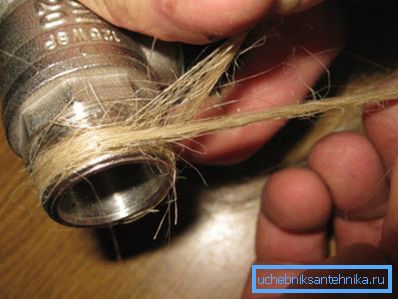
Tip! Beginners often make the mistake of thinking that the stronger the thread is tightened, the tighter the joint will be. In fact, with excessive effort, there is a risk of "dragging", breaking the thread and getting a guaranteed leakage.
Under the flange
For mounting parts with a diameter of more than 50 mm, flanges for pipes are used.
An example of such a fitting is shown in the image in this section.
- As a rule, these products are selected under the cross section of the pipeline. Also, sometimes flange joints are welded directly to the pipes, but in this case the reliability of the assembly is greatly reduced.
- For sealing in place of contact can be installed gasket of elastic material. In this case, the joint of two pipes requires periodic maintenance to replace a worn part.
- The advantage of flange fittings is the fact that they can be used to install shut-off valves, various sensors, valves, etc. on large-diameter pipelines.
Crimped
Relatively recently, so-called compression fittings have been used to connect metal pipes.
Their principle of operation is almost identical to that used when using a compression fitting for a plastic pipe:
- A cap nut made of metal (steel or brass) is installed on the thread.
- When screwing the nut, it presses a special gasket made of an elastic material or thin metal to the interface.
Note! The use of rubber or polymer pads imposes a limitation on the temperature conditions in which the system can be used: maximum heating is 950WITH.
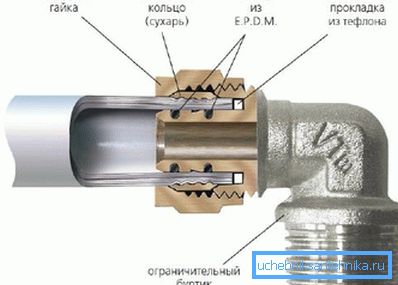
- At the same time, due to pressure, tightness is ensured for the functioning of the system.
- Some companies produce universal models of such devices, which are equally well suited for steel and plastic pipes.
Products of this type are usually used in the arrangement of water supply systems. The main advantage in this case is a significant gain in time: the pipe is put into a fitting without threading, which greatly facilitates our work.
On the other hand, such an installation scheme has its drawbacks. For example, with a serious effort, the pipe can simply be pulled out, especially if the gasket is somewhat shrunken and has lost elasticity. Of course, such a force vector is atypical for pipelines, but it is necessary to remember this feature!
Conclusion
Assembling metal communications with our own hands, we need to choose not only the pipes themselves, but also the parts that will be used to dock them. That is why it is important, before starting work, to familiarize yourself with the entire range of fittings available, and select those that will most closely correspond to the tasks set, our requirements and financial capabilities.
A more detailed overview of the products described above can be found on the video in this article.