Hdpe pipe - views and features
Low-pressure polyethylene pipes (HDPE) are a modern and widely demanded material for laying various types of pipelines. For example, a PND pipe according to GOST 18599 2001 can be used for pressure water pipes and gas pipelines. In this article we will take a closer look at the features of these products, areas of application and methods of installation.
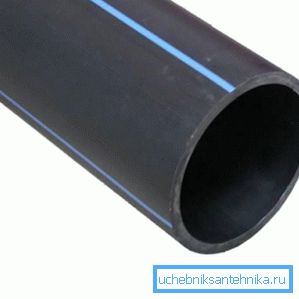
Special features
Properties
The characteristics of the HDPE pipe are primarily determined by the properties of the polyethylene from which it is made.
In particular, it is possible to distinguish:
- Resistance to alkalis and acids;
- With increasing material density, resistance to organic solvents is improved.;
- Corrosion Resistance;
- Environmental friendliness, so that the pipeline from the HDPE can be used to transport drinking water;
- Has the flexibility;
- Low thermal conductivity;
- Low weight of HDPE pipe,what simplifies its transportation and installation;
- Long service life;
- Resistance to low temperatures, unlike polypropylene polyvinyl chloride analogues. Moreover, in the case of a freezing system, the pipes do not lose their integrity, and can function after thawing.
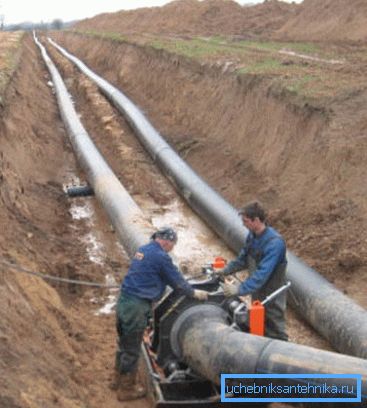
Of course, the material has not only positive qualities, but also some negative ones.
Among its shortcomings can be identified:
- High degree of thermal expansion;
- Instability to sunlight, which can reduce the life of the pipe.
- Oxygen permeability, resulting in air leaks into the plumbing system, which can create certain problems in heating systems.
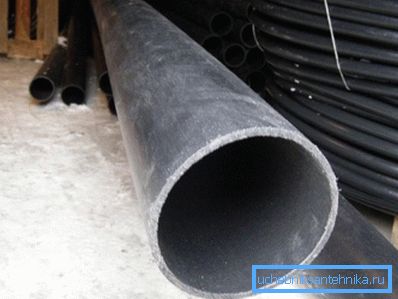
Note! Pipeline products made of cross-linked polyethylene are deprived of the latter drawback, although their price is higher.
These technical characteristics of the HDPE pipe limit its use in some areas, but for this reason they can effectively be used in others. Next, consider in more detail the cases in which its use is most appropriate.
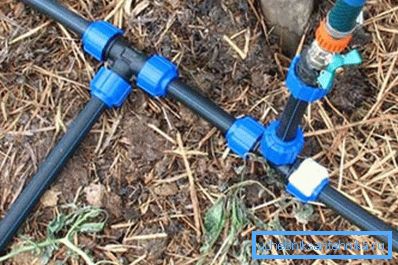
Application area
So, PND-pipes in the best way proved in the following scopes:
- Internal water supply;
- External plumbing;
- Gas supply;
- External pressure and non-pressure sewage;
- Internal sewage.
Note! Often beginner masters confuse polyethylene pipes LDPE and HDPE. Their main difference is plasticity. More flexible material is LDPE - HDPE pipe is more rigid, since the density of this material is higher.
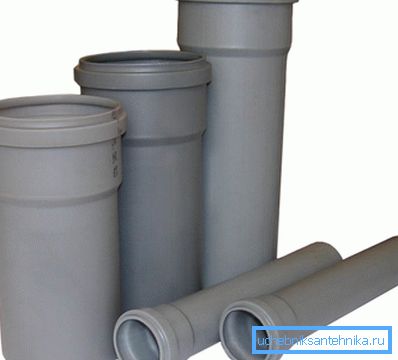
But in the heating system, the use of HDPE pipes is much more limited, as, indeed, in the hot water system.
Since under the influence of high temperature, the pipe changes its size quite strongly, to prevent negative phenomena, the following tricks are used in the systems:
- Installation is performed on "sliding" fasteners (in the case of an open gasket).
- Perform special compensation loops that reduce the linear expansion coefficient of the pipeline.
- In addition, in the manufacture of products, manufacturers add special additives to raw materials that can reduce the coefficient of linear expansion.
But there are some positive aspects of the use of such pipes in heating systems. For example, due to the low thermal conductivity, during transportation of the coolant polyethylene pipe provides minimal energy loss. Therefore, in heating systems often use risers made of HDPE pipes with a small coefficient of expansion.
It should be noted that, in spite of frost resistance, the pipes in question cannot be mounted in an open way without insulation. The fact is that the material can withstand a limited number of freezing and thawing cycles. In addition, the water plug will block the pipeline until it is thawed.
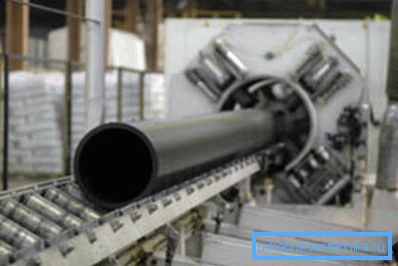
Production features
Today, the production of HDPE pipes is carried out in three ways:
Pneumatic formation | The polymer is fed into the mold under pneumatic pressure, with the result that the raw material is formed into a pipe. |
Extrusion | The raw material is melted, after which the liquid mass is squeezed out of the extruder, and then drawn out. As a result, the polymer solidifies as a finished product. |
Injection molding | The polymer mass under high pressure is evenly distributed along the walls of the mold, as a result of which a pipe is formed. |
It must be said that, depending on the characteristics of the raw materials and the type of production, the characteristics of the products may be different. Therefore, for different applications, use different polyethylene pipes. To make the right choice, you need to understand the labeling, which we will see below.
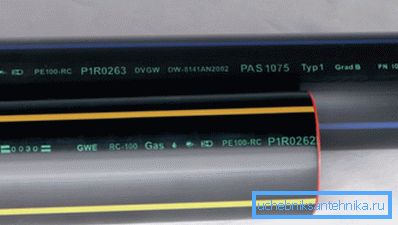
Marking
According to ISO requirements, a marking is applied to each running meter of the product, which contains the following information:
- Compliance with ISO9001 certificate;
- Who is the manufacturer of the product;
- In accordance with which GOST for HDPE pipes, the product was carried out;
- What type of material is used;
- Outside diameter;
- Wall thickness;
- Working pressure (nominal);
- Workspace;
- Allowable pressure;
- Batch number;
- Date of issue.
Installation
Installation of pipes PND can be carried out in two ways:
- Detachable, with the help of fittings - used in high-pressure pipelines.
- Non-detachable, with the help of a special apparatus - is used in pipelines with low pressure, for example, in sewers.
It must be said that regardless of the method of installation, it will not be difficult for even a non-expert to assemble the pipeline with their own hands. Next, we consider the features of each type.
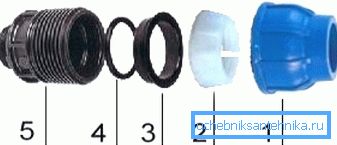
Split mounting
Detachable connection of the pipeline can be carried out in two ways:
- Bell fitting;
- With special fittings and pipe flanges.
Assembly of parts in both ways does not require special tools or fixtures. The only thing you might need is a wrench for tightening the clamping nuts. When assembling the pipeline using a bell-type method, silicone sealant is usually used to reliably seal the joints.
Tip! Home masters are often interested in how to bend or how to straighten the HDPE pipe, which may be required during the installation process. This problem can be solved by heating, since at a temperature of 80 degrees the material becomes autumn ductile.
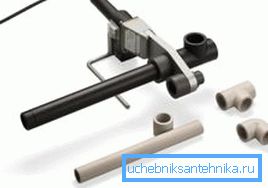
One-piece mounting
As mentioned above, for one-piece installation, you need a special welding machine (soldering iron). The principle of its operation is extremely simple - the device heats the ends of the parts to be connected to the melting temperature, after which it remains only to join them and wait for the polymer to harden.
Instructions for the implementation of this work is as follows:
- First of all, you need to connect the device to electricity and heat it up to operating temperature. A special indicator will inform you about the warm-up.
- Next, connect the parts to be inserted into the nozzle of the soldering iron and wait for the polymer to soften.
- After that, the parts are connected.
Tip! Before proceeding with the installation, you can practice on scraps of pipes, so as not to spoil the material.
Here, in fact, the whole process of installation.
Conclusion
On the basis of HDPE pipes, you can create efficient systems for transporting liquids and gases. The most important thing is to take into account the strengths and weaknesses of these products. For example, a HDPE pipe is an excellent material for cold water supply or even a pipeline transporting chemical fluids.
From the video in this article, you can get more information on this topic.