Pipe connections: pipelines and steel structures
What methods can be used to connect pipes in pressure and gravity pipelines? What ensures the tightness of the connection? On which fasteners can you assemble a rack or hanger for clothes made of chrome-plated pipes? Let's try to find answers to these questions.
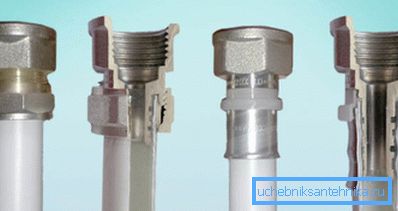
Classification
Let's start with the classification.
Connections can be:
- Hermetic and non-hermetic. It is obvious that the former are used in all pipelines without exception, the latter - in the assembly of various metal structures.
- Hermetic connections, in turn, are divided into pressure and non-pressure. The predominant field of application of the second - a variety of sewage systems: household, industrial and stormwater.
By the way: sewage can also be pressured. If it is necessary to transport the effluent up the slope, the fecal (drainage) pump assumes this function.
- In addition, the connection can be collapsible and non-collapsible.
Let us turn to specific solutions.
Sealed connections
Welding
The traditional way of connecting steel and, in recent years, plastic pipes is non-separable. The only way to dismantle a pipeline section is to cut it. How exactly the welding is carried out depends on the material being welded.
Steel
Steel pipelines are welded with gas and electric arc welding.
- In the first case, the flame of an acetylene torch melts the adjacent edges of the pipes, after which the welding wire introduced into the torch unites them with melt drops.
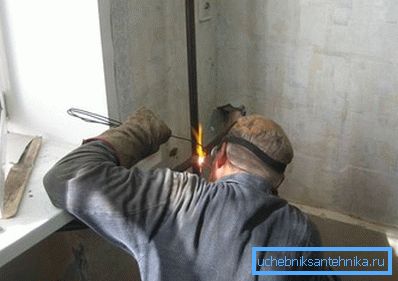
- In the second, the electric arc melts the welding electrode, the metal of which forms the seam. The dielectric coating of the electrode creates a layer of slag that protects the steel melt from contact with atmospheric oxygen and, accordingly, from the complete burning of carbon in it.
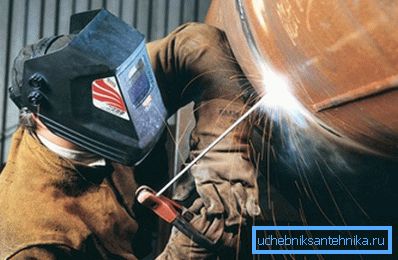
By the way: not only steel is welded by arc welding, but also cast iron. However, when installing pipelines from it, welding is usually not used, but cutting pipes with an arc at high currents is practiced.
The main problem of welded steel pipe joints is their vulnerability to corrosion. Even if zinc or any other layer of corrosion protection is initially present on the pipe surface, it burns out during the welding process. The problem is solved by protecting the seam area with the sprayed polymers, applying paints or coating with bitumen.
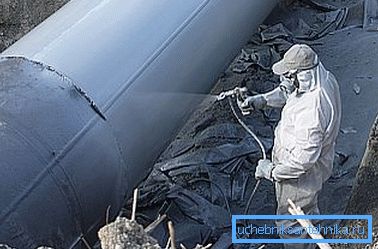
Polyethylene
Consider how to connect plastic pipes. Pipe connections are made end-to-end, with preliminary melting of the ends on a low-temperature heating element (mirror), heated to 200 - 220 degrees.
The list of basic technological operations is as follows:
- Tubes face strictly perpendicular to the longitudinal axis.
- The ends are cleaned of chips and dirt.
- The connected elements of the pipeline are centered.
- Then, the ends with a force of about 1.5 kgf / cm2 are pressed against the heating element equipped with an anti-adhesive coating.
- After melting, the mirror is removed from the future weld, while the pipes are pressed against each other for the time of precipitation and cooling of the polyethylene melt.
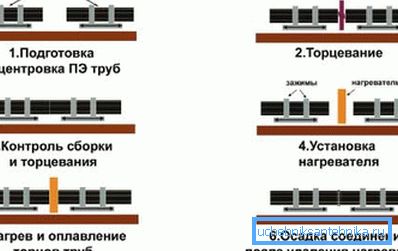
The heating and cooling time is related to the thickness of the pipeline walls.
Wall thickness mm | Duration of heating, s | The duration of cooling under pressure, min |
4.5 | 45 | 6 |
4.5 - 7 | 45 - 70 | 6 - 10 |
7 - 12 | 70 - 120 | 10 - 16 |
12 - 19 | 120 - 190 | 16 - 24 |
19 - 26 | 190 - 260 | 24 - 32 |
26 - 37 | 260 - 370 | 32 - 45 |
37 - 50 | 370 - 500 | 45 - 60 |
50 - 70 | 500 - 700 | 60 - 80 |
Since when aligning pipes with a considerable wall thickness, manual centering and clamping with the necessary effort are difficult, to put it mildly, mechanical devices are used for this purpose, and hydraulic devices with a diameter of 250 mm.
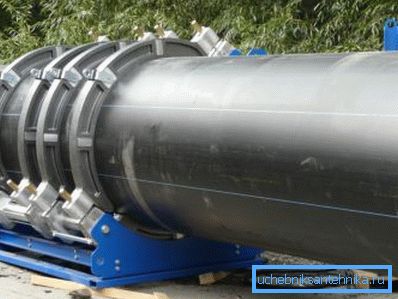
Polypropylene
Unlike polyethylene pipes, polypropylene pipes are not connected end-to-end, but by means of socket fittings. Low-temperature soldering iron pre-melts the adjacent surfaces of the pipe and fitting; the price of such devices starts from 800 - 1000 rubles. The heating time is not tied to the wall thickness, but to the diameter:
Outer diameter, mm | Duration of heating, s | Connection duration, sec | Cooling, min |
sixteen | five | four | 2 |
20 | 7 | ||
25 | 7 | ||
32 | eight | 6 | four |
40 | 12 | ||
50 | 18 | ||
63 | 24 | eight | 6 |
75 | thirty | ten | eight |
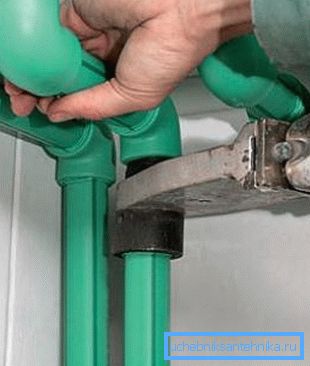
When assembling a polypropylene pipeline with your own hands, it is useful to know a few more subtleties.
- The temperature of the heating element in this case is higher than for polyethylene, and is 240 - 260C.
- The fitting is put on the pipe by a strictly forward movement, without rotation. Otherwise, there is a risk of receiving a wave on the surfaces being welded, which will sharply weaken the connection.
- The pipes reinforced with aluminum foil are preliminarily cleaned from it in the field of welding. Electrochemical decomposition of aluminum unprotected by a polymer layer may lead to the separation of the pipeline.
Soldering
Soldering pipes are practiced when assembling copper pipelines for various purposes.
The technology of soldering in brief is as follows:
- A socket is formed by rolling on one of the pipes to be joined.
- The end of the adjacent part (pipe or fitting) is inserted into it.
- The joined surfaces are heated in the flame of a gas burner and with the help of flux they are cleaned from the film of oxides.
- Then a solder rod is introduced into the burner flame. Due to the capillary effect, the melt fills the entire cavity between the socket and the pipe. By hardening, it makes the connection completely airtight.
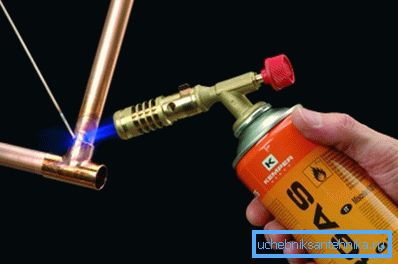
Threads
Threaded connections are another way of connecting pipes of small (up to 50 - 65 mm) diameter. What a threaded fitting looks like, I think, it is not necessary to explain to any person who lived in a Soviet-built apartment. Materials for them are quite traditional: cast iron, brass and, rarely, steel.
The sealing of the connection is ensured by its winding with flax fiber (often with paint or sealant), polymer threads or, in the case of gas pipelines, FUM tape.
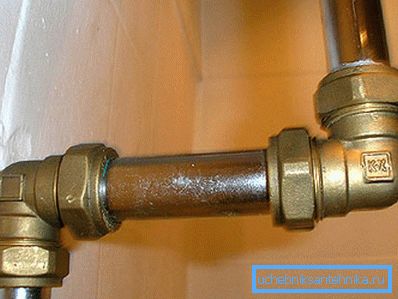
Flanges
It is obvious that the use of threads when installing a large diameter pipe is problematic. In this case, one more comparatively quick disconnect connection for pipes is used - flanged. Flanges bolted; tightness is ensured by a gasket between them - rubber, silicone or made of special heat-resistant rubber with a large amount of mineral filler - paronite.
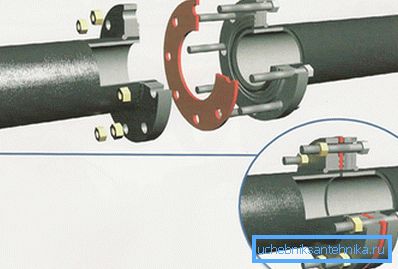
Bell fitting
In pressure and, more often, free-flow pipelines, bell-type installation is often used: the pipe is inserted into the socket of another pipe or fitting.
The problem of tightness can be solved in the following ways:
- O-ring rubber seal. This is how asbestos-cement pipes are connected, including pressure pipes; all types of plastic sewage; modern cast iron pipelines and pressure pipes made of polyvinyl chloride.
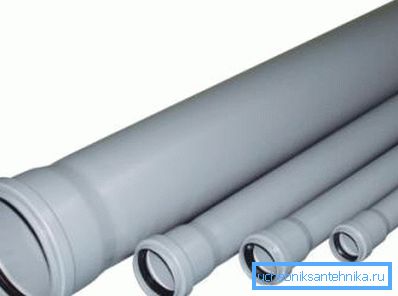
- Clay. In this way, along with ring seals, pressure PVC joints are sealed.
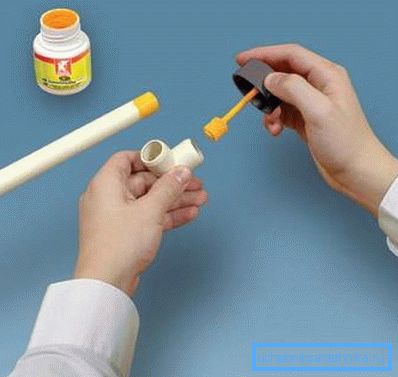
- Coinage. The organic fiber (cabol) soaked in bitumen or oil is compacted in the socket and sealed with cement mortar. This method of sealing was used for cast iron sewage throughout the 20th century.
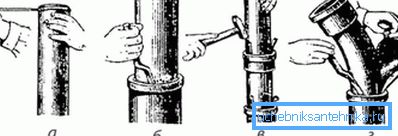
- Filling the bell with molten sulfur or lead. Sulfur was used for sewage, lead - for iron pipelines.
Fitting
For steel (including stainless), copper, polyethylene and metal-plastic, along with other fittings are used.
A list of what a pipe connector may look like in each case is the material for a separate large article; we mention only the main design solutions.
- Compression fitting compresses the pipe with an annular seal made of rubber or silicone when tightening the union nut with a conical internal section.
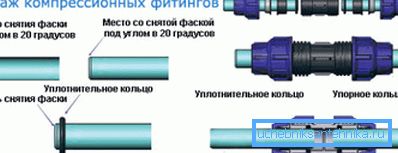
However: another scheme is used for soft copper and metal-plastic pipes. The fitting placed inside the pipe is crimped by its walls by means of a split ring.
- The press fitting uses pliers for crimping the pipe at the nozzle, which tighten the stainless steel sleeve.
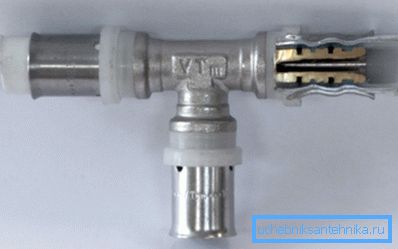
- The push-fit is the most convenient metal pipe connector to use. Installation instructions are ridiculously simple: you just need to push the end of the pipe into it with some effort. Tightness will provide an annular seal; Reverse movement prevents the ring spring with the feet fixing the pipe.
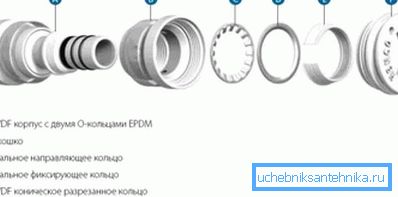
- Fitting stand for cross-linked polyethylene. These are the usual polymeric or brass fittings with an insertable sleeve. Cross-linked polyethylene has a mechanical memory and, after changing the diameter within a few minutes, returns to its original size, compressing the fitting; the sleeve only prevents disengagement when jerky.
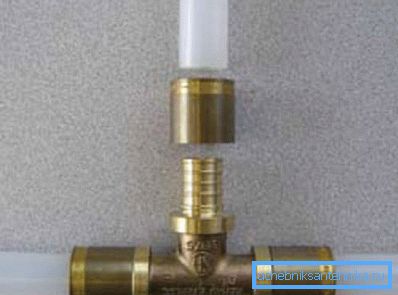
Unsealed connections
The connecting elements used for untight connections for structures made of pipes can be divided into two categories.
- In the first inserted tube is fixed with one or more screws. A fairly minor effort is required for fixation; however, the strength of the connection is also small.

- The second is all sorts of clamps. For the most part, they consist of two or more parts that are bolted together, crimping a circular or shaped pipe.

The appearance, size and shape of the connecting elements, of course, can be very diverse.
Conclusion
Of course, our material does not claim to cover all possible solutions. Something is probably left behind the scenes.
For more information on how a pipe connection might look like, the reader can learn more by viewing the video in this article. Successes!