Pipe made of tin - production in 3 steps on its own
Despite the many different tin blanks that are sold in building supermarkets, sometimes when installing drains, ventilation or other similar engineering systems, there is a need to install parts of non-standard configuration or size. Therefore, many home craftsmen are interested in how to make a pipe out of tin with their own hands.
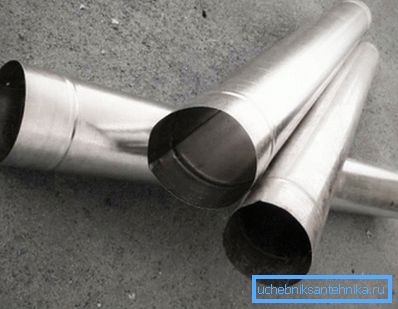
Features of the material used
Before starting work, it is advisable to carefully familiarize yourself with the characteristics of the material from which the pipe is to be constructed. Tin is an ordinary sheet of steel with a thickness of 0.1 to 0.7 mm. It is formed by successive rolling of the workpiece through the rollers of the rolling mill.
However, the processing does not end there. In order to protect the resulting sheet from the effects of corrosion, it is necessary to cover it with a layer of another substance that does not oxidize in air.
As a result, steel sheets, the width of which, according to GOST, can be 51.2-100 cm, covered with an ultrathin layer of zinc, chromium or tin, arrive at the finished product warehouse.
Note! The material is very plastic, which allows it to be processed at home. On the other hand, when arranging stiffeners, you can get a structure that is not inferior in strength to thicker steel.
Given that the price of tin is also low, it is often used to make many different parts of complex shape.
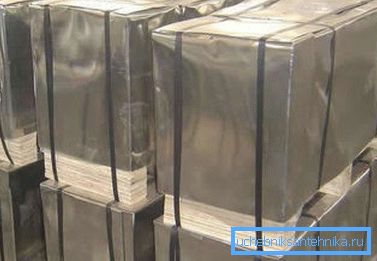
Required tools
For cutting and bending sheets of tin do not need to put a lot of effort. Nevertheless, it is useful to equip with special tools and devices, a list of which is given in the table.
Tool | Purpose |
Scissors for metal | Used to cut a sheet of tin into pieces of the required size. The maximum thickness of the material, as you know, is 0.7 mm; therefore, it is sufficient to apply only insignificant muscular effort. |
Mallet | You can replace it with a rubber hammer, as well as a steel tool with rubber pads that do not leave dents on the tin during use. |
Pliers | Used to make bends. Can be replaced with tongs. |
Crafting table | For marking and cutting it is necessary to place a sheet of tin on a flat surface. It is best to use a carpentry workbench, but you can also cut on the floor, cleaned from large debris. |
Calibration elements | Their role is performed by a thick-walled steel pipe with a diameter of about 100 mm (or round wood) and a steel corner 75 mm wide. It is fastened to the edge of the workbench or clamped in a woodwork vice. The pipe will be needed for the manufacture of a longitudinal seam of the pipe. |
Razmer | Used for marking on tin. It is a thin steel rod with a sharp end. |
Measuring tool | This includes rulers, roulettes, squares and other similar devices. |
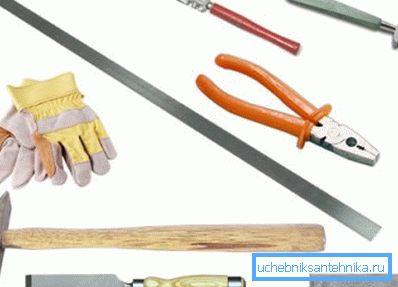
Work process
Let's start making a pipe from tin with our own hands.
The whole process can be divided into several main stages:
- Training. This includes the marking of the product and the cutting of individual blanks from a piece of tin.
- Molding. At this stage, the initial formation of a circular pipe takes place.
- Compound. Here it is necessary to finally sew the parts into the finished product.
Consider each of them in more detail.
Step 1. Preparation
Before you start making tin pipe, you should mark out and cut out the desired size of a large piece of tin. (See also the Exhaust Tubes: Features.)
Complex instructions are not needed here, everything is very simple:
- the sheet is placed on a flat area (workbench or floor);
- a length equal to the length of the future pipe is measured from the top edge (marks can be made with a marker or a special marker);
- then through the mark with the help of a square is drawn a line perpendicular to the upper edge of the sheet;
- on the upper edge and the line drawn at the bottom, the width of the workpiece is measured, which is equal to the length of the pipe circumference (and 15 mm should be added to this parameter to arrange the joint);
- All marks are joined, after which the resulting lines are cut.
Tip! Knowing the diameter of the pipe, you can easily calculate the circumference (workpiece width) using the well-known formula L =? D where? - 3.14, D - diameter of the future part.
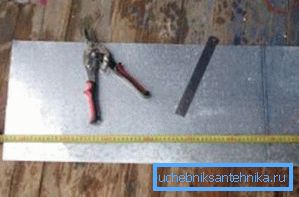
Step 2. Forming
After receiving the blank, it is necessary to form a circular profile of the future pipe.
Here the work is done as follows:
- Marked line for folds. Its width is 0.5 cm on one side and 1 on the other. Folds are bent at an angle of 90 degrees to the plane of the sheet of tin. To do this, you can use a steel corner and a mallet.
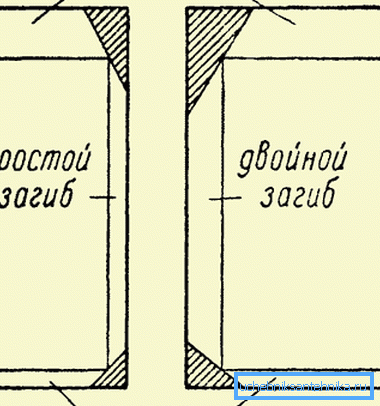
A sheet of tin is placed on the edge of the table with an offset to the desired length, then with a blow of a rubber hammer its edge is gently bent. At the end of the work, it should be in close contact with the lower plane of the angle.
Work should be done evenly along the entire length of the workpiece. To facilitate the procedure, you can use pliers.
- Then, on the centimeter fold, another bend is made in the shape of the letter G. The upper part (its width should be 0.5 cm) should be made parallel to the sheet of tin. It is desirable to make a markup for this bend in advance.

- At the end of the work with the folds, go to work on the pipe itself. For this, a pre-stored round part is used. Having placed a sheet of tin on it, it is necessary with the help of a mallet to give it a rounded shape. This should be done gradually over the entire length of the sheet until the bent edges meet.
Step 3. Docking
It remains only to combine the edges and secure the seam. To do this, the horizontal section of the larger fold folds down, closing the opposite edge. Then, the protruding seam bends to the plane of the pipe with the help of a mallet.
The bend must be done in the direction opposite to the L-shaped fold, otherwise water may get under the seam and, as a result, into the inner space of the pipe.
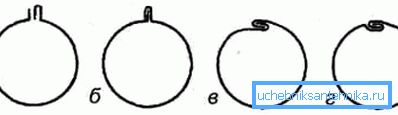
Useful tips
When working with tin, it is advisable to consider the following points:
- It will be more comfortable to work with metal shears if you attach a leather loop to one of the handles., which is worn on the fingers.
- Cut off the edge, it is desirable to process the plane from the old cloth for a hacksaw for metal. This will save the cut from burrs, which can be injured.
- To shorten the finished ventilation pipe can be used can opener.
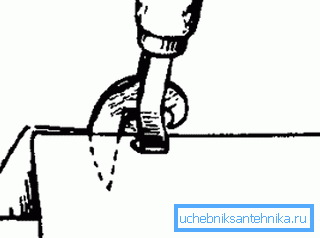
Conclusion
The process of manufacturing pipes from tin is quite simple, so if necessary, you can easily make the necessary part yourself. Similarly, it is possible to design a box for pipes. More details about this can be found in the video in this article.