Polyethylene pressure pipes - we study all their features
This material has already become the most popular in the field of laying various communications. Polyethylene pressure pipes are controlled according to GOST, which ensures excellent quality of these products.
We will tell you about them further.
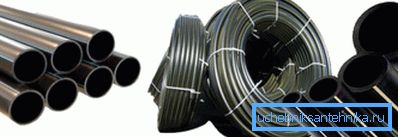
Special features
To have a complete picture of a product, it is necessary to have the fullness of information. Therefore, our instructions will tell you in detail about all the features of the product described by us.
Merits
First of all, we will publicize all the positive qualities, of which there are quite a lot (see also the article Heating a Pipe with a Heating Cable: How the Process Goes).
So, the main reasons for the popularity of this material are as follows:
- Very high wear resistance. As a result, a very long service life is about 50 years (despite the fact that for most competitors it does not exceed 25 years). In this case, tests have shown that many models can last much longer without losing their original qualities.
- Another equally important factor is the affordable price. In an era of constant crises, it is the economic factor that sometimes contributes to the growth of the popularity of a product.
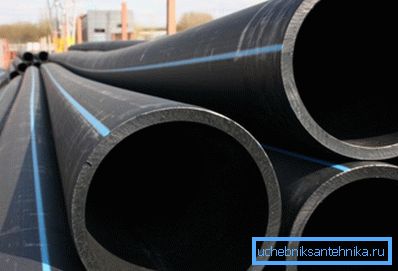
Interestingly, the production of such pipes involves fairly low financial and labor costs, affordable cost of raw materials and the ability to fully automate the process. These factors contributed to their low cost.
- We should not forget about the low coefficient of thermal conductivity, due to which such products look like an excellent option for laying hot water. It is also worth noting that no condensation appears on them.
- The widest range of sizes and shapes, allowing to solve any problems of laying. GOST 18599 83 for polyethylene pressure pipes regulates the main indicators, which prevents the purchase of low-quality products.
- Plasticity is perhaps the most important advantage, because no other material has such a property. As a result, they are not afraid of even the freezing of the liquid inside: the polyethylene will simply expand. Moreover, when the temperature rises, the product will take on its former shape.
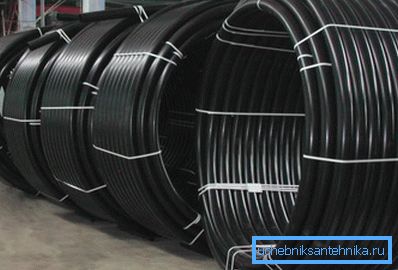
- Moreover, they are not even afraid of the drawdown of the building. Destruction will begin only at a strain value of more than 7% of the total length, which is very much. Note that this is the best indicator, among all the mass-used materials.
- Also, do not forget about the inertia that protects them from corrosion. Due to this, the laying of water supply pipelines from polyethylene pressure pipes turns out to be the most reliable and durable. In addition, they are completely impermeable to current, so they can even be used for power grids.
Interesting: in Japan at the legislative level, it is recommended to use the HDPE for laying communications. Recall that in this country there is increased seismic activity, it is from here that such a recommendation came out.
- Welding of such elements is much cheaper than metal. In addition, such an operation does not require special skills. She can cope with her hands with anyone, even a completely inexperienced person in such matters.
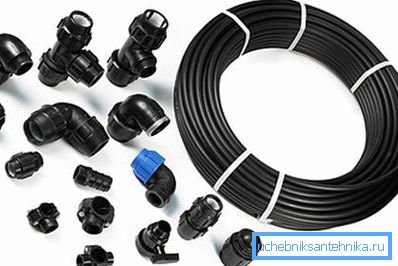
disadvantages
Everything in this world has flaws. In order to have a holistic opinion about something, it is necessary to know its negative sides.
Let's talk about them:
- Serious oxygen permeability.
- Low UV resistance. This factor makes it necessary to lay communications in such a way that sunlight does not fall on them in the future.
- Poor temperature resistance. If the liquid heats up to 100 degrees, then PE will simply melt. This factor greatly limits the scope of application.
Fastening methods
These products are connected by several techniques:
- Split parts - involves the use of special fittings (fasteners). This option allows you to safely disassemble if necessary. In order to choose the size of the flanges, look at the appropriate GOST for polyethylene pressure pipes.
- Butt Welding - used mainly for products with a diameter of more than 60 mm. They consist in heating the elements and their further joining, pressing “joint to joint”.
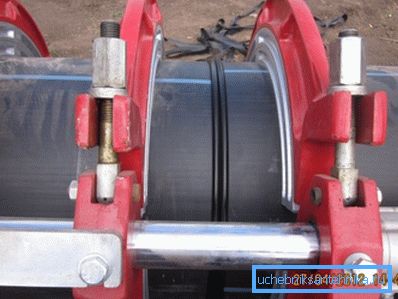
- Coupling welding - It is considered the most costly, and at the same time effective method. With it, you can achieve maximum tightness of pipes of any diameter. The use of electrofusion greatly facilitates the process.
A few words about state standards
Now consider GOST 18599 2001 for polyethylene pressure pipes. It controls the dimensions of products with high accuracy. This allows you to quietly "re-buy" the material if necessary.
There are four types of wall thickness:
- Light (marking - L): maximum pressure 0.25 MPa.
- Mid-light (SL): 0.4 MPa.
- Average (C): 0.6 MPa.
- Heavy (T): 1 MPa.
Based on this, consider the key assortment used today.
Outside diameter | Wall thickness (mm) | ||||
Nominal (cm) | Tolerances (mm) | L | SL | WITH | T |
one | 0.3 | - | - | - | 2 |
1.2 | - | - | - | 2 | |
1.6 | - | - | 2 | 2.7 | |
2 | - | - | 2.3 | 3.4 | |
2.5 | - | 2 | 2.8 | 4.2 | |
3.2 | 0.4 | 2 | 2.4 | 3.6 | 5.4 |
four | 2 | 3 | 4.5 | 6.7 | |
five | 0.5 | 2.4 | 3.7 | 5.6 | 8.3 |
6.3 | 3 | 4.7 | 7.1 | 10.5 |
Note! The maximum permissible deviation of the wall thickness is 0.4-0.7 mm, depending on the specific model.

At last
That ended our story, but we made sure that you get the most complete store of knowledge. In the presented video in this article you will find additional information on this topic (see also the article How the cable is laid independently in pipes of various types).
His viewing will allow to understand all the nuances.