Production of polyethylene pipes - reveal all the features
We live in an era of high technology and the creation of one or another material with improved characteristics is becoming increasingly affordable. Today, anyone can buy, for example, equipment for the production of polyethylene pipes and contribute to this aspect of the business.
We will tell you about all the nuances of this line.
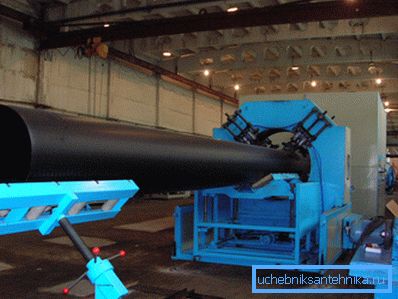
Production features
The creation of any material on an industrial scale has many features. Therefore, our instructions will tell you in detail about all the nuances.
Stages
The creation of such products is carried out by extrusion. This operation is a closed continuous loop, which is now fully automated.
Consider the sequence of actions.
- The supply of granules (raw materials) in a special bunker, which is located above the material cylinder. This procedure occurs automatically, that is, without human intervention.
- Then the granules are sent to the above-mentioned cylinder. There they are melted to the desired state.
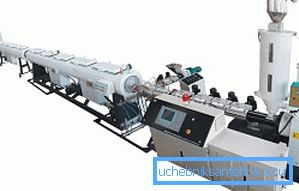
- Then they are delivered to the extrusion head with the help of a screw. There is a process of forming blanks.
- The material cylinder is heated to the desired temperature thanks to a special ring heaters. They are located on the surface of the cylinder.
- When the workpiece passes through the extrusion head, it is formed. Simply put, molten particles of polyethylene are transformed into a product that already looks like a pipe.
- After that, using a vacuum moulder, the existing billets are calibrated by diameter. At the same time, the wall thickness is adjusted, thanks to the change in the speed of the pulling machine.
- If it was possible to achieve the desired physical parameters, the available billet is sent to the tank (bath), where it is subjected to final cooling.
- When it is completely cooled and hardened, reconcile the footage using a counter.
- At the end of the resulting pipe is wound into a coil or cut.
As you can see, everything is extremely simple.
Quality control
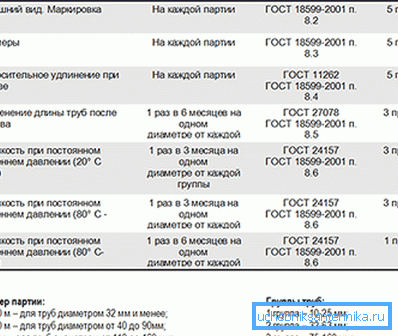
When the first batch came out, it must be subjected to quality control.
Usually experienced craftsmen do inspection with their own hands, paying attention to the following:
- Wall thickness. There must be a maximum measurement accuracy. In this case, measurements are made along the entire length of the product.
- External diameter.
- The level of ovality.
- The length of the segments. The least significant indicator.
The obtained data are compared with the parameters of GOST. If compliance is observed for all criteria, the batch is allowed for further packaging and distribution into classes.
Note! The closer to the standards of the main indicators, the higher should be the grade of the product.
After a visual inspection, more thorough laboratory tests follow. They allow you to study the chemical composition. Without such a procedure it is impossible to obtain the appropriate certification.
Equipment
Raw materials for the production of polyethylene pipes are special polymer granules. Most often black, but sometimes white. The key machine is an extruder that extrudes these elongated products.
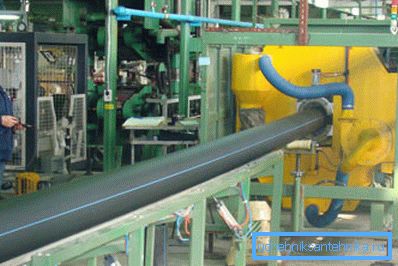
There are three types of this device:
- Screw. They work like a juicer (or meat grinder).
- Disk drives. The key work item is a disk. They are used mainly for products from a mixture of materials.
- Combined. Includes common features from both of the above types.
Most often, manufacturers of polyethylene pipes in Russia use the first variety. This is due to its relative availability and speed.
In addition to the extruder, the following equipment is involved in the production:
- The mechanism for the supply of raw materials.
- Pulling machine
- Mixer.
- Tank for calibration and cooling.
- Device for cutting blanks.
- Standard conveyor belt.
Note! From the power of the tape will largely depend on the speed of production.
- Vacuum Moulder
- The drive, which is designed for stacking finished products.
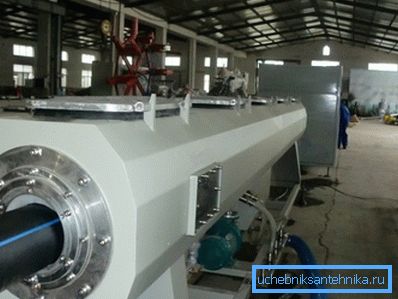
Please note: when changing suppliers, it is very likely that you will have to change at least some of the equipment. Otherwise, you will have to look for a supplier whose raw materials have the same chemical structure, which will be problematic in poorly developed (industrially) regions.
Today you can find a variety of equipment, the price of which can vary greatly. Experts say that it is better to give preference to more advanced counterparts. In their opinion, the return on such samples is much faster (despite the cost) due to high manufacturability.
Six reasons to open such a business
If you are thinking about opening such an enterprise, then we want to make public several factors “for”:
- Such products are very popular in our time. The twenty first century can be called the era of plastic. Therefore, its producers are unlikely to be left without bread.
Interesting: the EU countries decided to completely switch to plastic pipes for water supply. Today, about 80% of domestic water lines are implemented using the above-mentioned material.
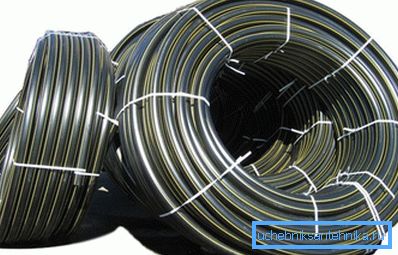
- Full process automation. You do not have to hire a large number of workers. All processes are performed without human assistance.
- Relatively low power consumption. At the initial stages of business, this factor plays a very important role.
- Waste-free production, which is also environmentally friendly.
- Compactness. For a standard installation, 100 square meters will be enough.
- Inexpensive raw materials.
At last
That ended our story, but we made sure that you get the most complete store of knowledge.
In the presented video in this article you will find additional information on this topic. His viewing will help to understand all the intricacies.