Sewer polyethylene pipes: features of the choice and
At about the end of the last century, sewage polyethylene pipes everywhere replaced metal and steel analogues. No, this does not mean that steel and cast iron are not used at all, but according to statistics, more than half of the sewer systems in modern residential and public buildings are made using polymeric materials.
The reason for the wide distribution of polymer systems, in the first place, has become an attractive price and a number of advantages, which we will discuss in this article.
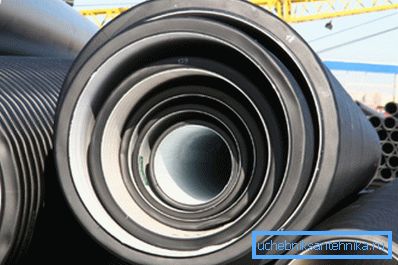
Main characteristics
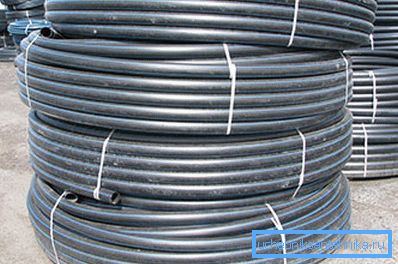
Polyethylene pipe for sewage is used in the construction of internal and external wastewater disposal systems. The main difference between the external and internal modifications is the long-term resistance to low temperatures.
Permissible operating condition parameters are indicated on the markings on the surface of the pipes. Therefore, with the choice of the desired option, there will be no difficulties.
Modern polyethylene sewer pipes are characterized by the following advantages:
- operational life of not less than 50 years, provided correct installation;
- operation without the need for regular maintenance;
- smooth inner surface of the walls, which contributes to a better passage of the transported liquid medium without sedimentation of contaminants;
- resistance to water hammering;
- absolute corrosion resistance;
- low weight and ease of machining, which greatly simplifies installation work;
- variety of sizes and configurations;
- wide range of fittings and fittings.
Polyethylene sewer pipes according to GOST 22689.2-89 are standardized in accordance with the following indicators:
- the degree of smoothness and flatness of the outer and inner surface;
- elongation at break during tests on the bench (as a rule, it is not less than 250%);
- nominal and maximum strength at permanent internal pressure;
- change of pipe sizes in the process of heating.
When choosing polymer pipes for the sewer system assembly, attention should be paid to the following specifications:
- nominal wall thickness;
- average outer diameter;
- the ratio of these sizes.
As a rule, on sale polyethylene pipes are presented in the form of segments with a length of 6-12 meters. At the same time in the construction industry used pipes up to 110 meters, rolled into coils.
Important: Long-term storage and operation of polyethylene pipes is allowed in places with a small amount of sunlight. Permanent exposure to direct sunlight can bring to the deformation of the pipe.
Features of the production process
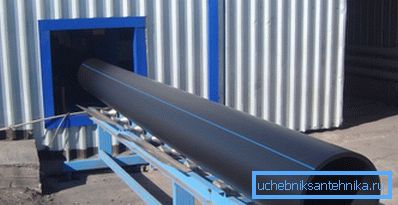
Technical characteristics of polyethylene pipes for sewage largely depend on the features of the implementation of the production process. Industrial production is carried out by extrusion.
The technological cycle includes the following operations:
- preparation of polyethylene mass and loading into an extruder;
- extrusion (a process during which a gradual extrusion of the mass through the forming nozzle is performed).
- submission of the workpiece to the calibrating nozzle;
- molding products in accordance with the established sizes and configuration;
- cooling the finished product;
- marking;
- packaging and storage of finished pipes.
Based on the characteristics of production methods, two types of polyethylene sewage pipes are distinguished:
- low pressure polyethylene (HDPE);
- high pressure polyethylene (LDPE).
In the manufacture of polymeric mass proceeds polymerization reaction of ethylene. In order for the reaction to proceed quickly, special conditions are created which are characterized by elevated pressure and high temperature.
In addition, catalysts are used, which also contribute to the acceleration of the reaction. If the production of polymer mass proceeds under conditions of high pressure, the finished polyethylene is called LDPE.
Products from such polyethylene are characterized by the following properties:
- low density and low resistance to mechanical deformations
- small weight and as a result simplicity of transportation and installation;
- resistance to the negative effects of aggressive environments;
- expediency of application at installation of the internal sewerage.
If the reaction proceeds at medium and low rates of pressure (not more than 2 MPa), the finished product is called PND and it is characterized by increased density and strength.
Special properties are distinguished by modern high-tech material, called “cross-linked” polyethylene. The main difference of the material is a unique molecular structure, providing not only enhanced strength properties, but also high resistance to critical high temperatures (melting point in the range from +360? C to +430? C).
The main types of sewer pipes made of polyethylene
Pressure pipes are universally used for the installation of pressure sewer systems and water mains. At production the PE-80 polymer is used. Corrugated pipes are used in the assembly of external sewer systems.
These products are distinguished by a two-layer structure, where the upper corrugated layer performs the function of stiffeners. The inner layer is an ideally smooth surface of the walls, which excludes the deposition of solid particles and the formation of blockages.
Such pipes are made of two types of PE80 and PE63 polyethylene. Both brands are resistant to chemicals.
Features of the installation work
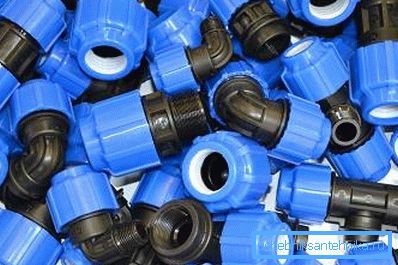
Modern polyethylene pipes for sewage according to GOST require installation using three main types of connections:
- Connections of bell-shaped type are the most demanded today both at professional carrying out installation works, and at construction of the sewerage with the hands. Installation instructions are simple, it is enough to insert a pipe with a rolled end into the fitting socket and twisting it around its axis, push it as far as it will go and move it back 1-2 mm.
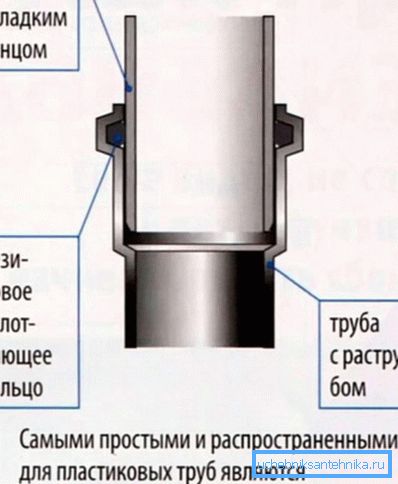
Tip: For ease of installation, the surface of the pipe can be smeared with soapy water.
The advantage of this type of installation is the absence of the need for a special installation tool. In addition, even an inexperienced plumber will probably cope with such work.
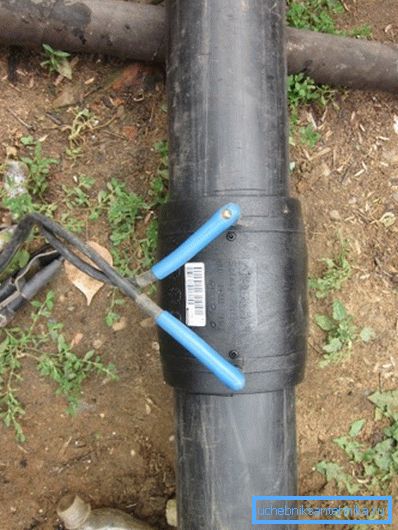
- Welded joint is mainly required for the construction of small diameter pipelines. Welding is carried out by means of a special apparatus, which heats the pipe and fitting, which are subsequently connected and, as the seam cools, form a strong and tight joint.
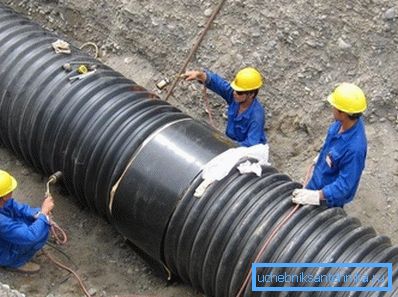
- Coupling type coupling is mainly used when working with corrugated pipes.. In this case, a special sliding sleeve is put on top of the joint. In order for the joints in the recess of the corrugations under the clutch to be sufficiently tight, rubber seals are installed.
Conclusion
Now you know what sewer pipes are and why they are popular. Moreover, now you know what the installation instructions are and you will be able to apply this knowledge in practice.
More useful information can be found by watching the video in this article.