Steel pipe diameters: studying standards
Despite the proliferation of modern composite materials, steel remains in demand in the manufacture of pipelines for various purposes. What can be the diameters of steel pipes according to GOST? In general, what standards regulate their production? Where and for what are appropriate products used? Let's figure it out.
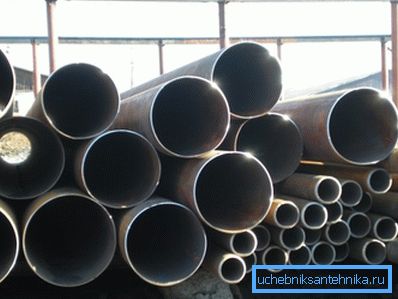
Regulations
Let's start with a list of standards that we have to study.
- According to GOST 3262-75 products for water and gas pipelines are manufactured.
- Pump and pipeline pipelines (NKT) are mounted from rolled metal produced in accordance with GOST 633-80.
- The range of seamless hot-rolled pipes is contained in the standard number 8732-78.
- For cold deformed product range is normalized according to GOST 9734-75.
- Welded pipes for gas and oil lines are produced according to GOST 20295-85.
- Finally, steel pipes of large diameters for gas pipelines, oil pipelines and oil pipelines are manufactured in accordance with GOST R 52079-2003.
Please note: this list does not claim to cover all areas of production. We have deliberately excluded some specific products like casing pipes or pipe frames for the automotive industry.
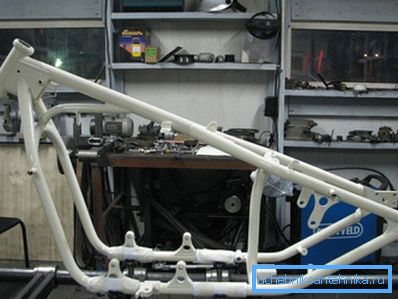
Sizes and applications
So, what are the diameters of steel pipes in accordance with these documents? For what purpose is the pipe used?
GOST 3262-75
The full list of sizes provided by the standard is relatively small, so we will give it in full.
Conditional pass | Outside diameter | Pipe wall thickness | ||
Lungs | Common | Amplified | ||
6 | 10.2 | 1.8 | 2.0 | 2.5 |
eight | 13.5 | 2.0 | 2.2 | 2.8 |
ten | 17.0 | 2.0 | 2.2 | 2.8 |
15 | 21.3 | 2.5 | 2.8 | 3.2 |
20 | 26,8 | 2.5 | 2.8 | 3.2 |
25 | 33.6 | 2.8 | 3.2 | 4.0 |
32 | 42.3 | 2.8 | 3.2 | 4.0 |
40 | 48.0 | 3.0 | 3.5 | 4.0 |
50 | 60.0 | 3.0 | 3.5 | 4.5 |
65 | 75.5 | 3.2 | 4.0 | 4.5 |
80 | 88.5 | 3.5 | 4.0 | 4.5 |
90 | 101.3 | 3.5 | 4.0 | 4.5 |
100 | 114.0 | 4.0 | 4.5 | 5.0 |
125 | 140.0 | 4.0 | 4.5 | 5.5 |
150 | 165.0 | 4.0 | 4.5 | 5.5 |
Products can be made with anti-corrosion zinc coating and without it. In addition, they can be supplied with chopped or knurled threads.
A scope - distributing of water supply, gas and heating within residential, office and production buildings.
Let's give some examples of use.
- A diameter of 15 mm is in demand as water supply and gas in-house connections.
- A steel pipe of 20 mm is used as a supply to radiators.
- Steel pipe 25 mm is used for installation of heating pipes.
- Steel pipe 40 mm is suitable for bottling heating and water supply.
- A steel pipe of 125 mm is suitable for the installation of hot-water pipelines, and a couple of decades earlier - and cold-water pipelines.
For reference: a steel pipe of 8 mm, 6 and 10 mm, if used in water and gas pipelines, is incredibly skillfully hidden. In the rich practice of the masters of our project, these dimensions have never met.
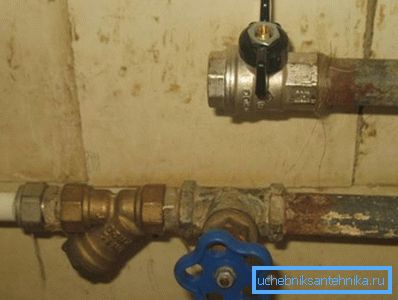
The price of VGP pipes is one of the lowest among all pipe rolled products due to the use of low-cost steel grades and production technology: high-frequency currents are used for welding, which ensures minimal time costs per meter.
GOST 633-80
The list of the assortment stipulated by this regulatory document does not strike with its size either.
Nominal diameter, mm | Wall thickness mm |
27 | 3.0 |
33 | 3.5 |
42 | 3.5 |
48 | 4.0 |
60 | 5.0 |
73 | 5.5; 7.0 |
89 | 6.5; 8.0 |
102 | 6.5 |
114 | 7.0 |
What else is useful to know about products manufactured according to the norms of this standard:
- According to the production technology, they can be only and exclusively seamless, that is, obtained not by twisting a flat billet (strip), but by flashing a solid steel cylinder (rod). This production method provides significantly greater resistance to internal hydraulic pressure: electric welding seam is always inferior to the strength of the whole metal.
- The pipe is produced as smooth (under the connection of couplings), and without clutch, with ends landed outside.
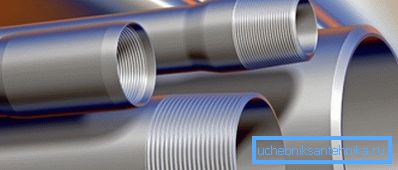
- Products with screwed and clutchless couplings must withstand hydraulic tests; at the same time, the internal pressure during testing is tied to the size of the pipe and varies from 375 to 1250 kgf / cm2.
For reference: the water pressure at the output of mining monitors reaches three times smaller values - no more than 400 kgf / cm2. The jet of such a monitor easily cuts rocks.
The use of tubing pipes mainly comes down to oil and gas production: they serve to pump natural hydrocarbons and create reservoir pressure.
GOST 8732-78
Seamless hot-rolled pipe can have a diameter of from 20 to 530 mm with a wall thickness of from 1.08 to 75 millimeters.
The technology of its production in brief is as follows:
- The cylindrical billet is heated in an induction furnace to a temperature at which the steel becomes plastic.
- On the piercing mill, it turns into a sleeve - a hollow cylinder.
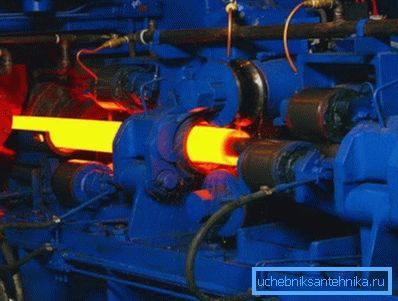
- After reheating, the workpiece, worn on the mandrel, passes a sequence of rollers, reducing its outer diameter.
- After cooling, the finished pipe is cut into segments and after passing the quality control is sent to the finished product warehouse.
Production for obvious reasons, has the highest energy intensity. In addition, due to the thick walls of the product are extremely massive: if the reinforced water-gas steel pipe of 65 mm weighs 7.88 kg / linear meter, then the hot-deformed 63.5x14 closest to it in diameter is as much as 17.09.
Where are hot rolled products used? It is clear that it is not for the construction of the suburban water supply system with their own hands: their strength here is clearly excessive. The main areas of application are high pressure pipelines and hydraulic systems.
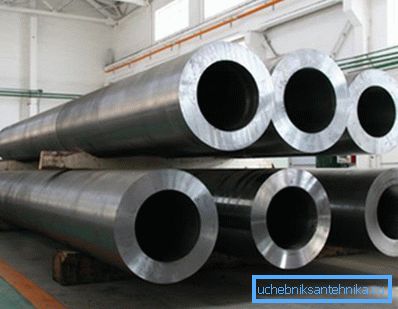
GOST 8734-75
The method of cold deformation differs from hot rolling only in that after the piercing mill the sleeve cools and further operations take place at a temperature well below the point of steel recrystallization.
Since internal stresses inevitably accumulate during rolling in a metal, the instruction on production technology contained in one of the related standards requires mandatory heat treatment of the rolled metal after rolling: the steel heats up and slowly cools, acquiring viscosity and ductility.
What sizes are written in the standard:
- Diameter - from 5 to 250 mm.
- Wall thickness - from 0.3 to 24 mm. In this case, several options correspond to the same diameter: say, a steel pipe 200 mm can have walls from 3 to maximum 24 mm, and a steel pipe 110 mm - from 1.5 to 18.
As well as hot-rolled, cold-formed products are used where maximum resistance to hydraulic pressure with minimum weight is necessary.
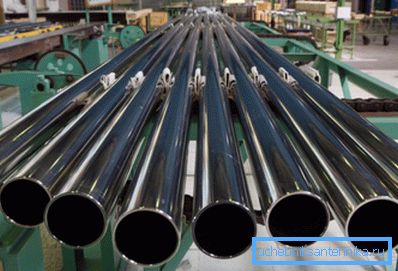
GOST 20295-85
The standard provides for the production of longitudinal and spiral-welded products with an outer diameter from 159 to 8220 mm with walls of 3 - 12 mm.
In this case, the standard contains recommendations on the method of manufacture for different size ranges:
- With a diameter of 159 - 426, it is permissible to use welding with high frequency currents.
- Electric arc welding of spiral joints can be used in the range of 159-820.
- Longitudinal arc welding is applicable for sizes 530-820.
GOST R 52079-2003
The last document in our list provides diameters from 114 to 1420 mm with walls from 3 to 21. And in this case, high-frequency welding with one longitudinal seam (dimensions 114-530), spiral-seam arc welding (159-1420) and longitudinal seam welding can be used with one or two longitudinal seams (530-1420 mm).
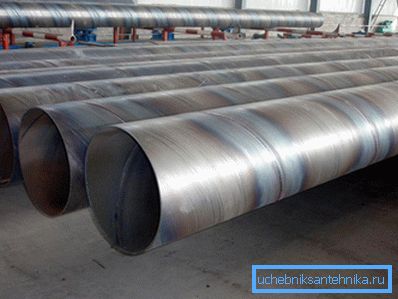
Conclusion
As already mentioned, our list of regulatory documents does not claim to be complete. For example, a 300 mm steel pipe does not correspond to any of the ranges mentioned; However, in the real price lists of manufacturers and dealers it is.
As always, the reader can find additional information in the video in this article. Successes!