The technology of welding pipes by different methods:
In this article we will look at the technology of welding large diameter pipes using modern equipment. The topic of the article is of considerable interest, since everywhere, from time to time, repair-restoration or construction works are carried out with the replacement of sewage, plumbing and heating systems.
When working with trunk pipelines, one cannot do without methods of welding joints carried out on large diameters. Again, the topic that will be considered in the article is interesting, since along with traditional metal pipes, polymer analogs have appeared, the combination of which presupposes the use of other methods.
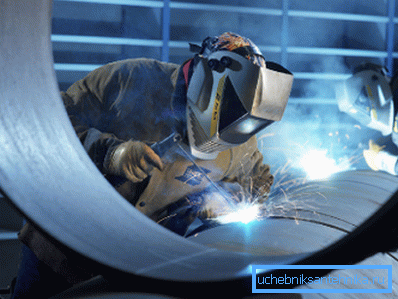
Therefore, before considering the main methods of pipe welding, we will consider the main modifications of large diameter pipelines that can be welded together.
Construction features of large diameter pipelines
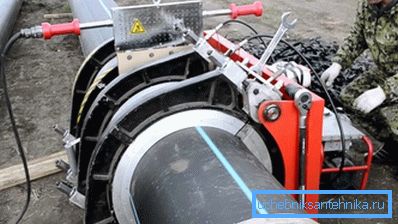
Instructions for welding work largely depends on the diameter of the pipes used. Large pipes include products with an external diameter of 530 mm and more.
Such products are used in the process of construction of main pipelines intended for transporting oil, gas, water, coolant from a centralized heating system and sewage.
All pipes of large diameter, suitable for connection by welding, can be divided into two broad categories:
- Hardware, which include round electric welded longitudinal and spiral steel pipes;
- Polymer products, which include a wide range of products made of polyethylene (PE), polypropylene (PP) and polyvinyl chloride (PVC).
Each of the listed pipe categories is connected using appropriate methods and suitable equipment.
Metallic Pipeline Assembly Methods
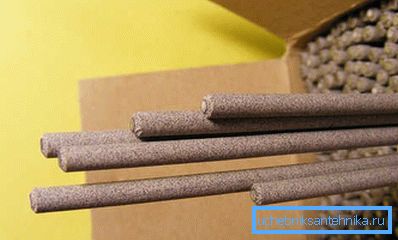
Regardless of what you have to do, be it welding pipes to the light or using more technologically advanced methods, it is assumed that the metal is heated to form an almost homogeneous and reliable joint. Therefore, in any case, you will have to work with special equipment, the use of which requires the need for proper professionalism and experience in performing welding works.
Consider the most popular welding methods that are commonly used when installing metal pipelines for various purposes.
Gas welding applications
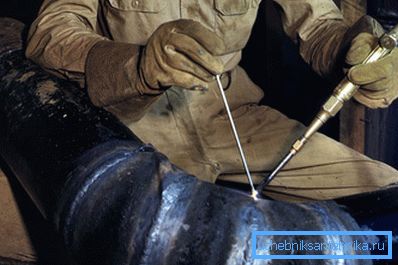
Gas pipe welding is a popular, time-tested method of joining metal parts in order to obtain a high-quality, strong and durable weld.
The principle of gas welding is as follows:
- the edge of the welded transverse sections is heated by means of a gas-oxygen flame;
- the gap between the two heated surfaces is filled with a metal bar melting during welding.
Important: The strength characteristics of the seam obtained in gas welding are lower than in electric arc welding. The choice of gas welded joint is justified in the event that it is necessary to work with thin-walled (up to 3.5 mm) pipes.

During the work with metal rolling with use of a gas torch the following materials are applied:
- Acetylene is a gas that is responsible for burning.
- Oxygen is a gas that provides the required combustion temperature and flame stability.
Important: In some cases, acetylene can be replaced by other flammable gases, such as propane or methane. The only condition that must be met is to maintain a higher temperature of the flame of the burner in comparison with the melting point of the metal.
- Filler material is needed to fill the weld. This material is selected in accordance with the chemical and physical properties of the metals being processed.
- Flux is used to prevent metal oxidation during heating. The fluxes in the form of a paste or powder, being deposited on the heated edges of the pipes, form a protective film that prevents oxygen from entering the structure of the seam.
The use of flux is necessary when working with most metals with the exception of carbon steels.
Electric arc welding
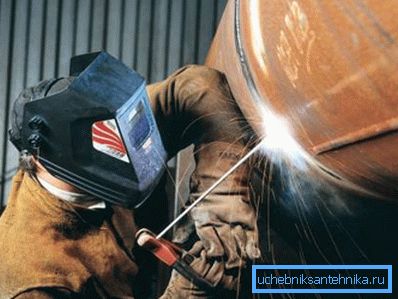
Electric arc pipe welding is a technology based on the heating of metal surfaces to operating temperature by means of electric arc discharge and subsequent fusion to produce a strong, reliable weld.
The electric arc technique has been known for a long time, and therefore many different more or less effective ways of making such a welded joint have been developed.
When working with large and medium diameter pipes, butt welding received the greatest popularity, when both transverse joints come close together and are centered, after which the formation of a seam occurs.
In accordance with the length, interrupted and solid seams are distinguished. High-quality boiling of a metal with a continuous seam requires a highly qualified specialist and an impressive experience in carrying out such work.
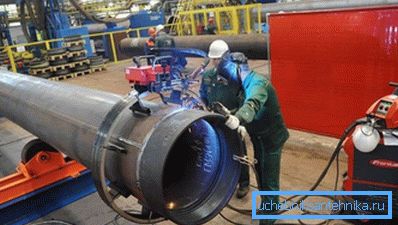
The technological development of manual electric arc technology has become orbital pipe welding, which has found wide application in the formation of non-rotary joints on medium and large diameter pipelines.
The process is based on arc welding with electrodes in inert gases. The use of a protective gas, such as argon, can prevent melting of the electrode.
Using certain gas mixtures can increase the speed and depth of penetration. As a rule, an inert mixture of argon with helium is used to obtain a very clean weld bead.
Orbital welding of stainless steel pipes or their conventional steel counterparts involves the use of two essential components:
- The current source from which power is fed and the current supply, the rotation of the electrodes, the supply of inert gas and wire are monitored. Most often, the current source is used inverter, because it is simple and effective in use.
- The orbital head, by means of which the electrode rotates around the pipe and the whole working cycle occurs.
Thanks to the joint operation of these two components, it becomes possible to mechanize the use of this equipment to obtain the optimum quality of the seam.
Orbital pipe welding has a number of significant advantages over the manual process:
- reasonable price of the finished result;
- less laboriousness of the process and, as a result, short deadlines for accomplishing the task;
- economic consumption of electrodes;
- the ability to work with different wall thickness with consistently high quality results;
- smooth and tight seam around the entire circumference, which is not easy to achieve by operating manually.
The use of laser welding
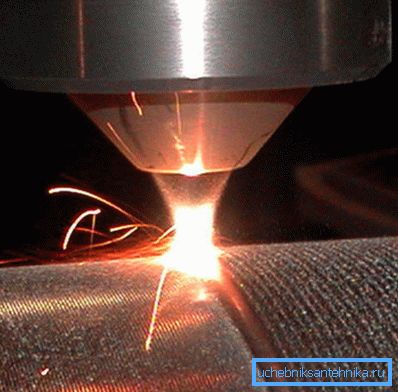
Laser pipe welding is a high-tech technique, which is based on melting metal using a light beam. Radiation for heating a metal surface is monochromatic with a wavelength depending on the nature of the working body of the laser emitter.
The efficiency of laser welding is determined by such parameters as:
- radiation power;
- focus spot diameter and configuration;
- the rate of movement of the workpiece relative to the laser beam.
Among the advantages of the technology we note the following:
- high intensity spot heating of the metal pipe until the melting temperature is reached.
- rapid cooling of the treated joint as radiation exposure ceases.
- minimum joint width without compromising the strength of the joint.
However, there are disadvantages, including:
- high cost of equipment due to novelty and small distribution of technology;
- the ability to work with hardware with a wall thickness of not more than 1-1.5 mm.
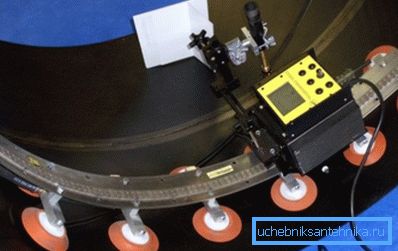
A standard laser welding machine consists of such key elements as an active medium and a pump generator.
By type of active environment, the devices are divided into the following categories:
- gas;
- solid-state;
- semiconductor.
Each of the listed modifications can be applied when assembling high-quality domestic pipelines, but no more than that, since the wall of trunk systems is most often thicker than 2 mm.
Welding swivel, rotary and horizontal joints
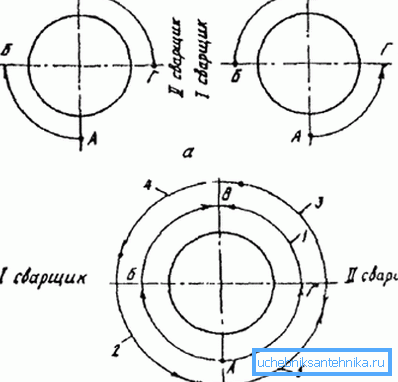
Rotary tube welding is necessary when assembling most large and medium-sized pipelines.
Welding is performed in three layers:
- at the initial stage, the joint is conditionally divided into four segments;
- then the first two segments are boiled, after which a 180 degree turn is made;
- then the remaining two segments are welded;
- the pipe is rotated ninety degrees and the second layer is being cooked;
- at the final stage, the pipe turns back 180 degrees and the joint is finally welded.
Welding of non-rotary joints is also performed in three layers. Fixed joints are boiled back and forth. It uses a short (no more than 2 mm) arc.
Welding of horizontal joints is performed with electrodes with a diameter of 4 mm. As in the previous case, the electrode moves back and forth during the formation of the seam. The result is a roller, the height of which does not exceed 1.5 mm.
The joint is boiled in three or four layers. During the formation of the last rollers, the diameter of the electrodes used is increased to 5 mm at a current of up to 300 A.
Tip: If this is not about assembling a new water supply system, but about fixing a leak in the old system, cold welding for heating pipes or water supply may be useful. In fact, it is a kind of epoxy glue with metal fragments dissolved in it. The elimination of leaks with your own hands can only be carried out on dry, previously cleaned from the pipes.
Of course, the use of cold welding in this case is only a temporary measure, after which a quality repair of the damaged pipe should be carried out.
Polymer Pipe Welding Methods
The technology of working with polymer pipes is fundamentally different from the welding of metal products.
At assembly of polymeric pipelines two most demanded methods are applied:
- The technology of butt joint involves heating and subsequent melting of the ends of the pipes to the operating temperature, and compression up to the formation of a hermetic seam. The welding process is carried out using special equipment consisting of a frame, centralizers and a heating element.
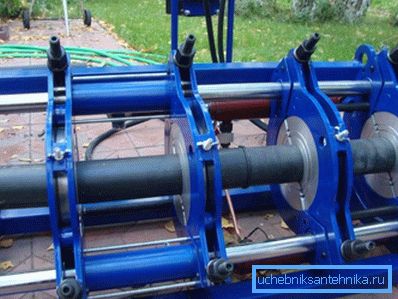
Devices for butt joining of polymer pipes are multifunctional and allow you to simultaneously adjust, and after that, center the cut of the joined ends before the subsequent heating. Heated to the operating temperature of the pipe shifted by a mechanized system of jacks.
The use of special machines allows you to perform welding work, both in stationary and in field conditions with obviously high quality of the joint.
- The technology of electrofusion connection allows to do without complex equipment, since the heating element is part of the coupling for welding pipes.
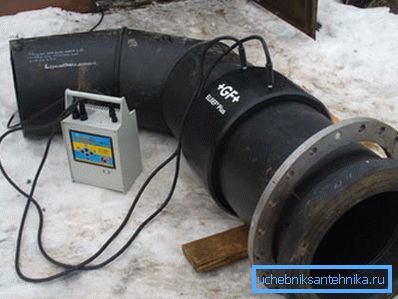
A polymer sleeve with a fused coil is put on the joint of the pipes to be joined, after which the coil is energized and the plastic is fused, forming a reliable and tight joint.
Conclusion
So, we have considered the features of welded joints used in the assembly of various large-diameter pipelines, both metal and polymer. Still have questions that could not be answered? In this case, more useful information can be found by watching the video in this article.